Floating production storage and offloading (FPSO) units are on the upward trend in the oil and gas industry because of their flexibility to meet changing demands in an unpredictable market. Yet, without good preservation strategies during construction and delivery, FPSO fabricators and owners can be in for a negative surprise when they encounter corrosion problems during FPSO commissioning or thereafter. VpCI® Technologies offer practical and effective solutions to avoid these unwanted corrosion-related downtime episodes to promote smoother commissioning and better durability.
A Corrosive Environment
FPSO topside equipment is often built near ocean ports and spends the rest of its service life in a marine environment. High temperatures, humidity, and salt spray create a perfect atmosphere for corrosion propagation. To make matters worse, certain types of equipment must be flushed or hydrotested during construction and commissioning, introducing corrosives that threaten to compromise the internal integrity of the equipment. For FPSO fabricators, the consequences are more serious than simply failing to deliver goods with a pleasing appearance. Far worse, corrosion on critical equipment can delay commissioning or cause more serious problems down the road, including high-cost, emergency shutdowns from corrosion-related failures on turbines or electrical systems. While corrosion consequences can be drastic, a few simple preservation strategies in key areas will go a long way toward preserving equipment until the time of commissioning.
Preserving Electricals and Electronics
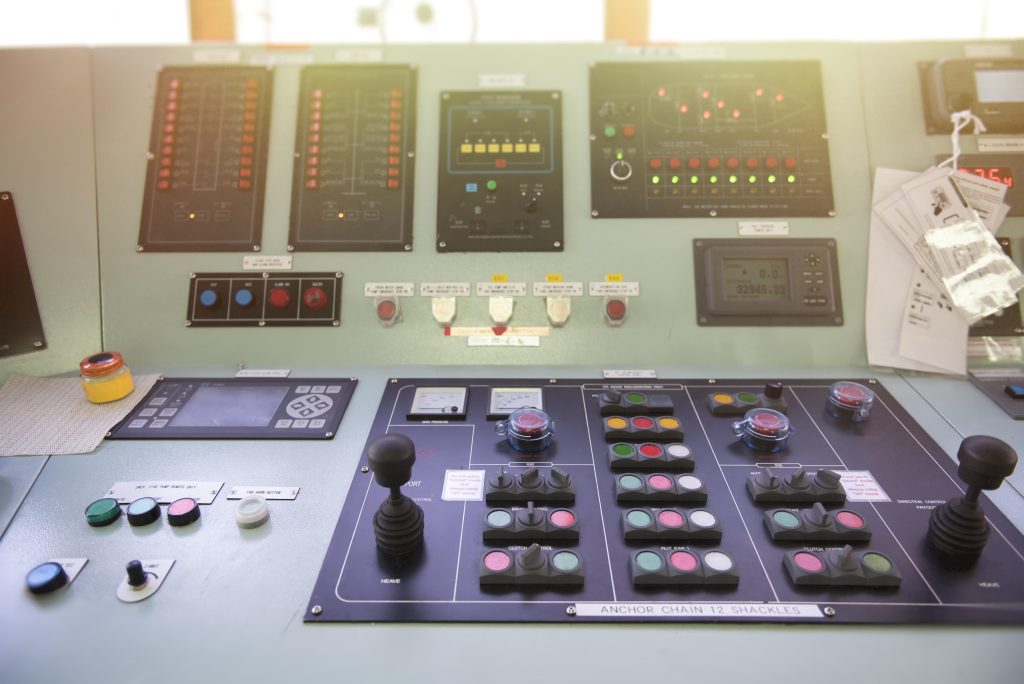
Electricals and electronics are the brains and nerve centers of a FPSO. Without them, operations would halt. Fortunately, electronics and electricals are some of the easiest components to protect by placing VpCI® Emitters inside the housings. VpCI® Emitters comes in multiple sizes—from the VpCI®-101 Device that protects 1 ft³ (28 L) of space to the VpCI®-308 Pouch that protects 35.3 ft³ (1 m³)—and release Vapor phase Corrosion Inhibitors that fill the enclosure, adsorbing on metal surfaces as a protective molecular layer. A quick spray of ElectriCorr™ VpCI®-239 on electrical connections—especially those that are not enclosed—offers added protection. These materials typically do not interfere with electrical/electronic operation and can often be left in place for ongoing corrosion protection during everyday use.
Protection During Hydrotesting
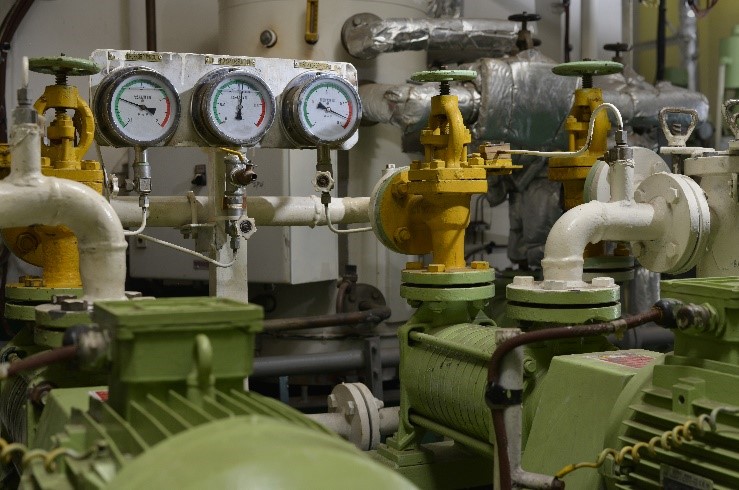
In addition to electronics, FPSOs encompass many fluid systems, including piping, pumps, valves, and compressor skids that may need to be hydrotested or flushed. This activity can introduce moisture and sometimes even chlorides (e.g., if seawater is used) and is a prime opportunity to apply corrosion protection. Products such as those in the VpCI®-649 Series can be added to the hydrotest water for protection during hydrostatic testing and can be dosed at higher concentrations for extended periods of preservation. These hydrotest additives are both film-forming and vapor-phase corrosion inhibiting for protection of hard-to-reach areas inside valves or systems that are capped subsequent to hydrotesting.
Preserving Tanks, Vessels, and Flow Paths
Another means of internal protection is to apply VpCI®-337 or CorroLogic® Fogging Fluid VpCI®-339 . These Vapor phase Corrosion Inhibitors can be fogged into flow paths of gas turbines and other rotating equipment. They also work inside tanks, vessels, and other enclosed voids that could otherwise be difficult to protect. Removal is usually not needed prior to commissioning. If fogging is not preferred for one reason or another, VpCI®-308 Pouches can be placed inside the voids to release Vapor phase Corrosion Inhibitors through a breathable packaging membrane. These pouches can be taken out quite easily before equipment commissioning.
External Protection
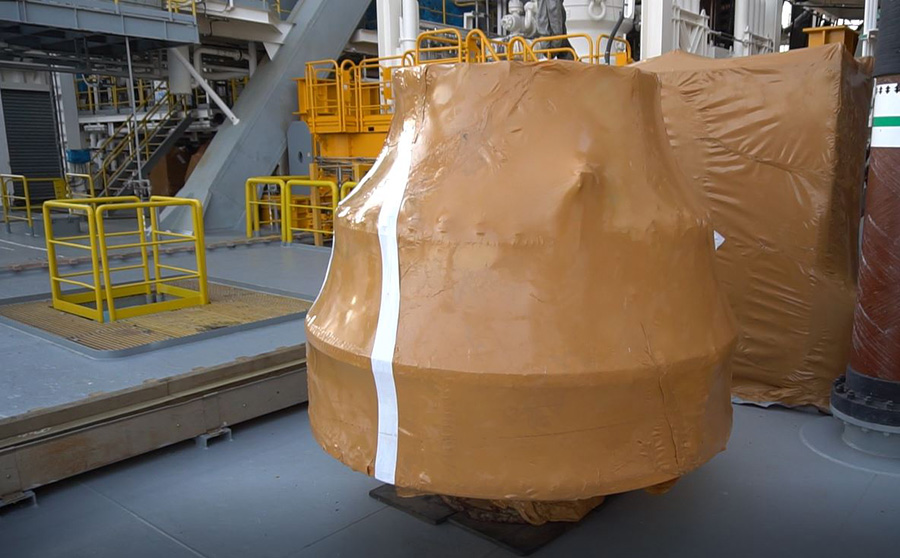
Turbines and other equipment fogged with VpCI® Technology are often wrapped in VpCI® Films such as VpCI®-126 HP UV Shrink Film and MilCorr® VpCI® Shrink Film—both to protect equipment externals and to trap Vapor phase Corrosion Inhibitors inside the equipment. Films are better than tarps for protection in outdoor environments because they create a barrier to external elements and contain corrosion inhibitors to actively mitigate corrosion. If needed, they can be fitted with access panels for easier inspection during the preservation period.
The Moment of Truth
Commissioning is the moment of truth when the relative success of preservation is revealed. Fortunately, Cortec® VpCI® Technologies are not only highly effective at inhibiting corrosion but also typically require little to no removal effort before the equipment can be used, promoting maximum uptime by streamlining the commissioning process. If you are interested in applying similar preservation strategies, contact Cortec® today for help protecting FPSO modules from corrosion until commissioning.