As battery-powered applications such as electric vehicles become more widespread, global demand for high-performance batteries, such as lithium-ion batteries, is also increasing. The challenge in manufacturing modern batteries is to maximize their energy density, reduce their manufacturing costs and extend their useful life. To achieve these goals, sensors from Micro-Epsilon are used throughout the entire manufacturing process. They perform various measurement tasks for machine monitoring, thickness control and quality assurance.
Modern battery cells should offer performance as well as being environmentally friendly and sustainable on the road. The long-term goal is to move cars, buses, vans, as well as construction machinery and trucks away from fossil fuels and towards electric drives based on battery and fuel cell technology. The revolution of previous drives has long been heralded, and the production processes are running at full speed. To increase the performance of energy storage devices while saving valuable resources, manufacturing processes are becoming increasingly complex. This requires innovative, high precision sensors that monitor the automated manufacturing processes inline.
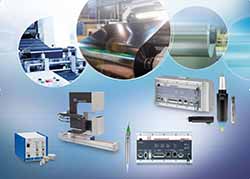
A lithium-ion cell passes through many stations before final assembly. Production can be divided into three main process stages: electrode fabrication, cell assembly, as well as formation and aging. Sensors from Micro-Epsilon are used in all important process stages to solve various measurement tasks. Micro-Epsilon offers a wide product range with the largest variety of physical measurement methods for precise displacement and distance measurements. What makes it special is that all of Micro-Epsilon’s sensor technologies are developed, manufactured and distributed in-house. Therefore, customer-specific adjustments to the sensors can also be implemented if required.
Coating:
Wet film thickness measurement of the anode and cathode materials
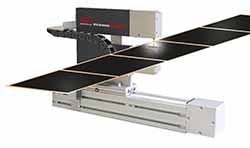
In the coating process, the film is coated either continuously or intermittently and over a width of up to 1000 mm. Important factors are the film and coating thickness, surface quality, cleanliness and avoidance of gas inclusions. To monitor the wet film thickness of the anode and cathode materials, an accuracy of <±1 μm is required at 150 to 500 µm object thickness. For this measurement task, it is recommended to use the thicknessGAUGE, which is an inline measuring system consisting of a linear unit with electromechanical drive, two confocal chromatic distance sensors, an automatic calibration unit and a multi-touch panel IPC. The confocal sensors measure the material surface from two sides using the differential method. Based on automatic calibration with a reference target, the distance between the two sensors is determined at regular intervals. The high precision of ±0.25 µm and the measuring rate of up to 5 kHz enable fully automated thickness measurement.
Drying:
Drying process of the anode and cathode materials
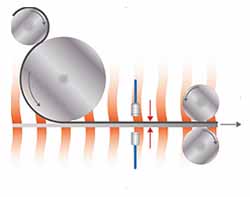
Following the coating process, the coated aluminum or copper film passes through the drying process. The drying speed is up to 100 m/min at 80 to 160 °C. After drying the anode and cathode materials, a thickness test is necessary for quality assurance. The required accuracy is 1 µm for a target thickness of 75 to 400 µm. Both confocal chromatic and capacitive sensors from Micro-Epsilon are particularly suitable for this measurement task. The sensors are optimized for industrial requirements, extremely compact and deliver the highest accuracy in the submicrometer range regardless of whether the surface is glossy or matt.
Similarly, Micro-Epsilon’s Sensors can be used in Calendering for Roller Gap Measurement with Calenders, in Edge Curvature after Cutting, in Cell Assembly for volume measurement when applying the hear conducting paste,Thermal Imaging Camera along with dedicated software in formation stage, etc.
Conclusion:
Micro-Epsilon offers a worldwide unique range of sensors, measurement systems and customized inspection systems. The wide product range, which is based on different measurement principles, is ideal for the production processes in demanding battery production. Micro-Epsilon’s high-precision sensors reliably measure displacement, distance, position, inclination, acceleration, color and temperature in order to achieve robot-assisted 3D inspection of both matt and glossy surfaces using high-tech inspection systems.