Light detection and ranging (LiDAR) applications include autonomous vehicles, drones, warehouse automation, and precision agriculture. Humans are present in most of these applications, leading to concerns about a LiDAR laser’s potential to cause eye damage. To prevent injury, automotive LiDAR systems must meet IEC 60825-1 Class 1 safety requirements while transmitting at up to 200 watts.
The general solution uses a pulse of 1 to 2 nanoseconds (ns) at a 1 to 2 megahertz (MHz) repetition rate. This is challenging as a microcontroller or other large digital integrated circuit (IC) is needed to control the laser diode but cannot directly drive it, so a gate driver circuit must be added. Also, this gate driver design must be optimized to ensure that the performance of the LiDAR system is suitable for Society of Automotive Engineers (SAE) Level 3 and higher advanced driver assistance (ADAS) systems.
Designing a high-power and high-performance gate driver that meets the safety requirements of IEC 60825-1 using discrete components is complex and time consuming, potentially adding to cost and extending time to market. To meet these challenges, designers can turn to integrated, high-speed gate driver ICs paired with gallium nitride (GaN) power field effect transistors (FETs). Using an integrated solution minimizes the parasitics that degrade the integrity of the drive signal, particularly in the high-current laser power loop, and it enables locating the high-current driver close to the power switches, minimizing the effect of high-frequency switching noise.
This article provides a brief introduction to LiDAR. It discusses applications and safety requirements before reviewing the challenges of designing automotive LiDAR, focusing on the high-current laser power loop. It then presents LiDAR solutions from Efficient Power Conversion (EPC), Excelitas Technologies, ams OSRAM, and Texas Instruments, including GaN power FETs, gate drivers, and laser diodes, along with evaluation boards and implementation guidance to speed the development process.
How LiDAR works
LiDAR systems measure the round-trip time-of-flight (ToF) (Δt) of a laser beam pulse to calculate the distance from an object (Figure 1). The distance (d) can be calculated using the formula d = c * Δt/2, where c is the speed of light in air. Short pulse durations are one of the keys to LiDAR. Given that the speed of light is approximately 30 centimeters per ns (cm/ns), a 1 ns LiDAR pulse has a length of about 30 cm. This puts a lower limit of about 15 cm on the minimum feature size that can be resolved. As a result, LiDAR pulses must be limited to a few nanoseconds to have a useful resolution for human-scale environments.
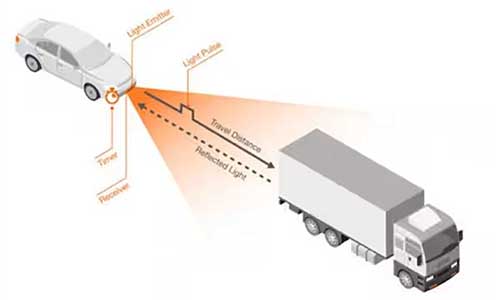
their distance. (Image source: ams OSRAM)
Pulse width, peak power, repetition frequency, and duty cycle are primary LiDAR specifications. For example, a typical laser diode used in a LiDAR system may have a pulse width of 100 ns or less, a peak power of >100 watts, a 1 kilohertz (kHz) or higher repetition frequency, and a duty cycle of 0.2%. The higher the peak power, the longer the detection range of the LiDAR, but thermal dissipation is a tradeoff. For a pulse width of 100 ns, the average duty cycle is usually limited to 0.1% to 0.2% to prevent laser overheating. Shorter pulse widths also contribute to LiDAR safety.
IEC 60825-1 defines laser safety in terms of the maximum permissible exposure (MPE), which is the highest energy density or power of a light source with negligible potential to cause eye damage. To be negligible, the MPE power level is limited to roughly 10% of the energy density, which has a 50% possibility of causing eye damage. With a constant power level, shorter pulse widths have a lower average energy density and are safer.
While a single LiDAR ToF measurement can determine the distance to an object, thousands or millions of LiDAR ToF measurements can be used to create a three-dimensional (3-D) point cloud (Figure 2). A point cloud is a collection of data points storing large amounts of information called components. Each component contains a value describing an attribute. The components may include x, y, and z coordinates and information about the intensity, color, and time (to measure object movement). LiDAR point clouds create a real-time 3-D model of the target area.
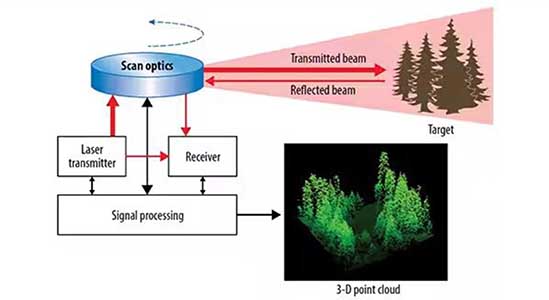
3-D point clouds and images of a target area. (Image source: EPC)
Use GaN FETs to power LiDAR lasers
GaN FETs switch much faster than their silicon counterparts, making them suitable for LiDAR applications requiring very narrow pulse widths. For example, the EPC2252 from EPC is an AEC-Q101 automotive-qualified 80 volt GaN FET capable of current pulses up to 75 amperes (A) (Figure 3). The EPC2252 has a maximum on resistance (RDS(on)) of 11 milliohms (mΩ), a maximum total gate charge (Qg) of 4.3 nanocoulombs (nC), and zero source-drain recovery charge (QRR).
The IC is delivered as a die-size ball grid array (DSBGA). This means the passivated die is directly attached to solder balls without any other packaging. As a result, the DSBGA chips are the same size as the silicon die, minimizing their form factor. In this case, the EPC2252 uses a 9-DSBGA implementation that measures 1.5 x 1.5 millimeters (mm). It has a thermal resistance of 8.3°C per watt (˚C/W) from junction to board, making it suitable for high-density systems.
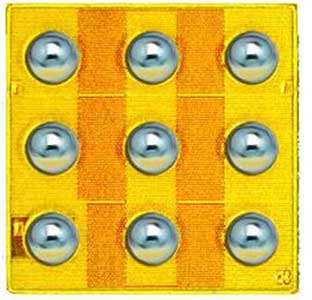
laser diodes in automotive LiDAR systems. (Image source: EPC)
Designers can use EPC’s EPC9179 development board for a fast start by employing the EPC2252 in LiDAR systems with total pulse widths of 2 to 3 ns (Figure 4). The EPC9179 includes an LMG1020 gate driver from Texas Instruments that can be controlled by an external signal or an onboard narrow-pulse generator (with sub-nanosecond precision).
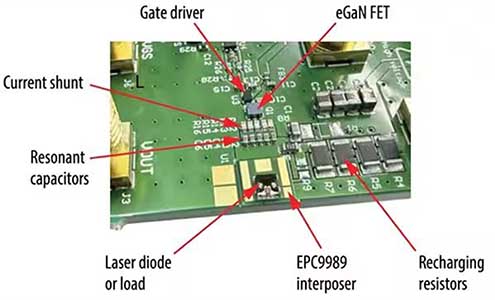
and other key components. (Image source: EPC)
The development board comes with an EPC9989 interposer board comprising break-away 5 x 5 mm interposers (Figure 5). These correspond to the mounting footprints of many common surface-mount laser diodes, such as SMD and MMCX, as well as the patterns designed to accommodate RF connectors and a wide variety of other loads.
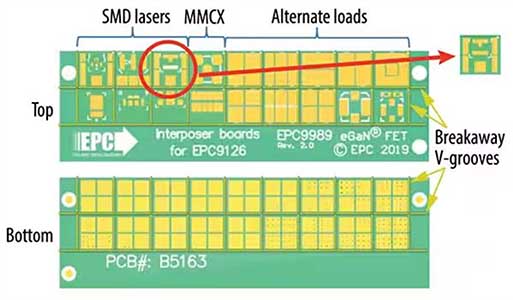
as the SMD laser interposer shown at the top right, that can be snapped off for
use with the EPC9179 demo board. (Image source: EPC)
Excelitas Technologies’ TPGAD1S09H pulsed laser (Figure 6), emitting at 905 nanometers (nm), can be used with the EPC9989 interposer board. This laser diode uses a multi-layer monolithic chip mounted on a leadless laminate carrier to provide excellent thermal performance with a wavelength temperature coefficient (Δλ/ΔT) of 0.25 nm/°C. This quantum-well laser supports rise and fall times of <1 ns with an appropriate driver. The TPGAD1S09H can be used in surface-mount applications and hybrid integration. It can emit light parallel or perpendicular to the mounting plane, and the epoxy resin encapsulation supports low-cost and high-volume manufacturing.
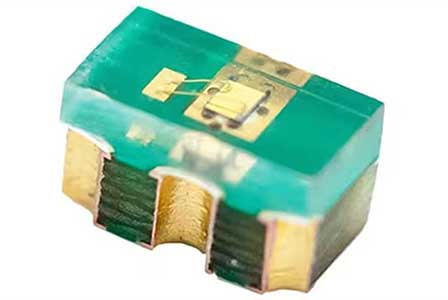
light parallel or perpendicular to the mounting plane. (Image source: Excelitas)
The SPL S1L90A_3 A01 from ams OSRAM (Figure 7) is another example of a laser diode that can be used with the EPC9989 interposer board. This single-channel 908 nm laser module can deliver pulses ranging from 1 to 100 ns with a peak output power of 120 watts. It supports an operating temperature range of -40 to +105°C with a duty cycle of 0.2% and comes in a compact QFN package measuring 2.0 x 2.3 x 0.69 mm.
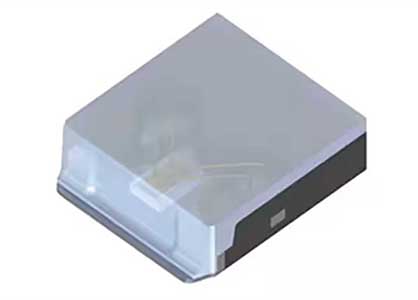
and can be used with the EPC9989 interposer board. (Image source: ams OSRAM)
For LiDAR systems that require extremely narrow pulse widths, designers can turn to Texas Instruments’ LMG1025-Q1, which is a single-channel, low-side gate driver with a 1.25 ns output pulse width capability that enables powerful LiDAR systems meeting IEC 60825-1 Class 1 safety requirements. Its narrow pulse width capability, fast switching, and 300 picoseconds (ps) pulse distortion enable precise LiDAR ToF measurements over a long range.
A propagation delay of 2.9 ns improves the control loop response time, and the 2 x 2 mm QFN package minimizes parasitic inductance, supporting high-current, low-ringing switching in high-frequency LiDAR drive circuits. The LMG1025-Q1EVM is an evaluation module for the LMG1025-Q1 that has a place to accommodate a resistive load to represent a typical laser diode, or for mounting a laser diode after drive pulse tuning with a resistive load (Figure 8).
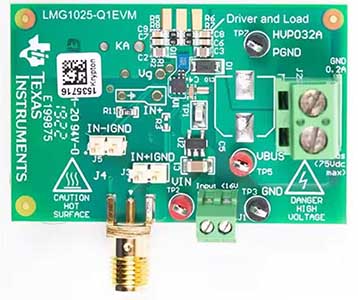
representing a typical laser diode for initial setup. (Image source: Texas Instruments)
Conclusion
Designers are increasingly challenged to develop automotive LiDAR systems that deliver real-time ToF measurements with centimeter resolution that meet the Class 1 safety requirements of IEC 60825-1. As shown, GaN FETs can be used with a variety of laser diodes to produce the nanosecond pulse widths and high peak-power levels needed in high-performance automotive LiDAR.