Leveraging 10Base-T1L SPE For IIoT Networks in Place of Legacy 4mA-20mA and Fieldbus
Introduction
Industrial controls and networking applications have mainly depended on 4mA-20mA and fieldbus connectivity with proprietary technologies serving higher speed or more specialized performance use cases. This solution has served many industrial applications well until recent years, when the rise of the Industrial Internet of Things (IIoT) and data-driven applications pushed the sensor, actuator, and controller device density and performance criteria to an all-time high. The new capabilities and use cases for IIoT applications are largely restricted by the 10Mbps limit of fieldbus networks, and growing demands are leading to the adoption of other industrial networking technologies to fill the gap. 10Base-T1L with single-pair Ethernet (SPE) is a promising replacement technology for many 4mA-20mA and fieldbus systems that need higher data rates. It also includes power delivery and a range of other attractive features. Of course, this new technology means different component requirements for common-mode chokes (CMCs), isolation inductors, and differential mode inductors (DMIs).
This blog discusses the use of 10Base-T1L and SPE in industrial applications and how this pairing can dramatically improve industrial network performance and unleash the latest IIoT technology. Additionally, we’ll consider reference designs and component requirements for 10Base-T1L and SPE implementations.
Ethernet and 10Base-T1L
SPE is a wired communication standard defined in IEEE 802.3 and effectively converts the basic Ethernet standard for use in a single-twisted wire pair. Power over data line (PoDL) is a standard for transmitting power over the same lines used for communication in order to minimize the wiring needed for power and communication. 10Base-T1L can transmit up to 10Mbps over 1000 meters in industrial applications and 15 meters in automotive or aeronautical applications. 10Base-T1L is defined by IEEE 802.3cg and has bandwidth capability from 0.1 to 20MHz.
PoDL was originally optimized for automotive and similar applications, where Power over Ethernet (PoE) was adopted for generic Ethernet applications. With clause 104 of IEEE 802.3, PoDL was expanded for 10Base-T1S/T1L with SPoE power classes 10 through 15, primarily for building automation and industrial networking systems. SPoE power classes are defined for operational technology (OT) networks, such as IIoT networks. SPoE has defined classes 10, 11, and 12 for long, medium, and short cables that use 20, 24, or 30VDC, respectively. Classes 13, 14, and 15 are also defined for long, medium, and short cables using 50, 55, and 58VDC, respectively. SPoE does not have a regulated or unregulated class like PoDL does, and thus SPoE can deliver between 1.23W to 52W of power (Table 1).
Table 1: IEEE 802.3 cg Power Classes for 10Base-T1L and SPoE. (Source: EPCOS / TDK)
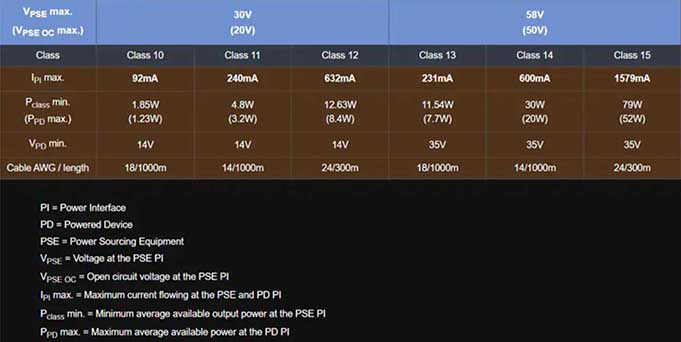
In essence, industrial Ethernet and commercial Ethernet are the same protocols. However, the hardware used to carry each protocol’s communication is completely different, with industrial Ethernet favoring more ruggedized hardware that is better optimized for extreme environments where reliability, chemical resistance, fire resistance, high/low operating temperature ranges, and other factors are necessary to consider. In many cases, commercial Ethernet hardware would suffer from limited lifetimes and potential early failure due to the nature of industrial environments and are therefore unsuited for industrial Ethernet applications.
Moreover, technologies such as 10Base-T1L are specifically designed for automotive, industrial, and building automation applications and support a suite of hardware options better suited for use cases in these environments than what commercial Ethernet is intended for. Where commercial Ethernet installations may benefit from running high-speed Ethernet cable amongst IT networking hardware throughout a facility, industrial applications will likely benefit more from running compact SPE using PoDL/SPoE to minimize cable bulk and add compatibility with legacy wiring infrastructure without adding excessive, unnecessary cabling. Fortunately, 10Base-T1L SPoE systems can provide IT/OT connectivity and power to sensors, actuators, or control hardware from the device to the cloud.
Implementation
To implement 10Base-T1L SPoE, it is necessary to use at least a common mode choke (CMC), but differential mode inductors (DMIs) and galvanic isolation transformers may also be necessary, depending on the application. If the application only requires data transmission between the control transceiver and the end device, then a CMC is needed between the twisted pair and the PHY/LPF controller. If power and data are to be transmitted along the same twisted pair, then a DMI will also be needed to bridge the power source equipment (PSE)—VCC and GND single-ended lines—to the twisted pair, which is best done before the CMC. Lastly, galvanic isolation is often required where there may be critical safety concerns. For this, an additional isolation transformer is needed between the PHY/LPF and the downstream circuitry for both the control and end-device hardware.
Figure 1 indicates where the DMI and CMC components are best placed in an 802.3cg-compliant circuit for class 10–14 applications. The power and data for this reference are coupled together at the medium-dependent interface (MDI) through the power coupling network (PCN). DC power is coupled into the SPoE line through a DMI, as seen at L1 in Figure 2. A CMC, seen at L2, provides the common mode blocking at the MDI. It is important to select DMI (L1) and CMC (L2) values to meet the return loss, mode conversion, and droop specifications listed in IEEE 802.3cg for the maximum power class.
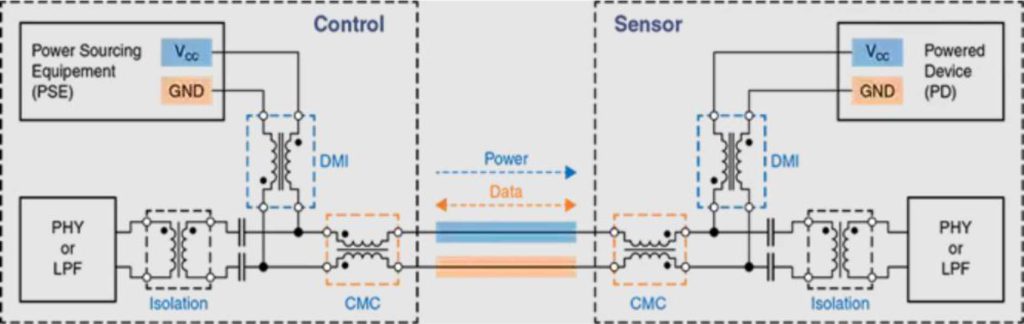
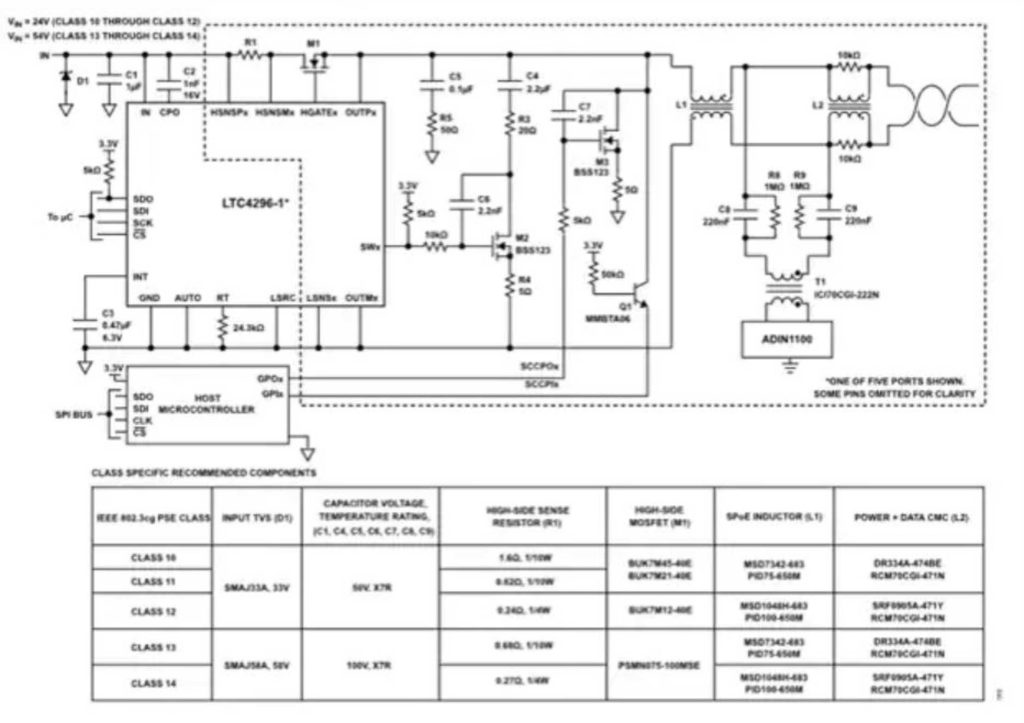
According to the manufacturer, the approach in Figure 2 is recommended for class 10 through 14 10Base-T1L SPoE applications, using a PHY-side PCN topology is the recommended approach, with power injected through the DMI (L1) on the PHY side of the CMC (L2). This allows for both power and data to be passed through the CMC. For class 15, it is recommended to inject power on the line side through the DMI with a separate CMC for both the power and data paths. EPCOS / TDK Industrial Single Power Ethernet (SPE) Inductors are ideally suited for these applications, hence their recommendation for use in SPoE PSE controller applications. These industrial SPE inductors are designed with the correct current, voltage, and inductance specifications for industrial SPE applications and are also ROHS compliant with operating temperatures ranging from -40°C to +125°C. EPCOS / TDK offers RCM70CGI-471 CMCs, ICI70CGI isolation inductors, and PID SMD Power Inductors, specifically fabricated for industrial SPE/SPoE applications.
Conclusion
As industrial automation expands to include higher data rate devices that demand more power and compatibility with intranet and the cloud, there is a greater need for industrial Ethernet solutions to provide data transmission and power to a host of emerging IIoT devices. 10Base-T1L is a prime candidate to replace legacy 4mA-20mA and fieldbus connectivity, as 10Base-T1L supports higher data rates, power over data lines, and additional features that exceed these legacy and other commercial Ethernet solutions.
Author
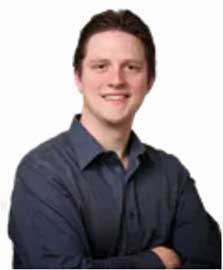
Principal of Information Exchange Services: Jean-Jacques DeLisle
Jean-Jacques (JJ) DeLisle attended the Rochester Institute of Technology, where he graduated with a BS and MS degree in Electrical Engineering. While studying, JJ pursued RF/microwave research, wrote for the university magazine, and was a member of the first improvisational comedy troupe @ RIT. Before completing his degree, JJ contracted as an IC layout and automated test design engineer for Synaptics Inc. After 6 years of original research—developing and characterizing intra-coaxial antennas and wireless sensor technology—JJ left RIT with several submitted technical papers and a US patent.
Further pursuing his career, JJ moved with his wife, Aalyia, to New York City. Here, he took on work as the Technical Engineering Editor for Microwaves & RF magazine. At the magazine, JJ learned how to merge his skills and passion for RF engineering and technical writing.
In the next phase of JJ’s career, he moved on to start his company, RFEMX, seeing a significant need in the industry for technically competent writers and objective industry experts. Progressing with that aim, JJ expanded his companies scope and vision and started Information Exchange Services (IXS).