Basingstoke, U. K., 15 March 2024 – From 14 to 16 May, manufacturers and users of optotechnology and image processing will once again gather in Frankfurt for the 16th Optatec. The leading trade fair for optical solutions, components and systems impresses with its high level of internationality and showcases top technologies at the highest level. It goes without saying that Aerotech will be there: at stand 711 in hall 3.1, the motion control experts will be presenting Infinite Field of View (IFOV), a pioneering solution for synchronising linear or rotary servo axes with the laser scanner. With Automation1, they also have the right motion control platform, whose intuitive user-friendliness visitors to the trade fair will also be able to familiarise themselves with. Finally, the HEX150, currently the most precise hexapod on the market according to Aerotech, will also be on display.
Aerotech has been supplying standard components and solutions such as motors, drives, controls, positioning tables, galvo scanners and much more for more than 50 years. Customised motion subsystems include positioning systems on granite structures with a base frame and vibration isolation, as well as external measuring systems. “Optatec, which takes place every two years, is a real industry highlight and the ideal stage for us to present our latest applications and manufacturing systems to a broad specialist audience”, says Simon Smith, European Director at Aerotech. “Many high-calibre experts and decision-makers come together in Frankfurt – this creates valuable synergies and numerous opportunities to make important contacts and meet potential customers.”
IFOV in laser processing
They will also be able to see Aerotech’s “Infinite Field of View (IFOV)” for themselves at the trade fair stand. This is an innovative solution for synchronising linear or rotating servo axes with laser scanners. By combining highly dynamic galvo scanners with the travel path of servo axes, parts that are significantly larger than the traditional field of view of a scanner can be processed continuously without having to link individual work areas together.
According to Aerotech, this leads to higher throughput rates. Stitching errors and quality problems with individual parts due to overlapping or uneven laser processing are also eliminated.
“With IFOV, we improve both the processing quality and the throughput of large parts,” explains Aerotech European Director Simon Smith. Users can select the best optics configuration for their application in no time at all, without having to compromise on the working area. “IFOV not only automatically increases the working area for each galvo system beyond what is possible with optics alone, but also eliminates the trade-offs between laser spot size and available working area by expanding the field of view regardless of the optics selection,” continues Simon Smith.
High accuracy and maximum user-friendliness
IFOV works smoothly every time without the user having to adjust parameters and settings for different motion paths. This is because IFOV uses a single controller to process the 2D profile requested by the user and convert it into the relative servo stage movement and the scanner movement in real time. IFOV takes into account the available working range of the scanner to ensure that the commanded trajectory remains within the field of view.
In addition, the acceleration and current limits of the servo and scanner axes are taken into account so that the commanded movement does not cause any error states on one of the axes. The combined movement ensures that the tool path specified by the user is precisely maintained.
Since IFOV uses a standardised, open control architecture, the actual feedback information is shared in the controller and made available to the user. As a result, the movement of the scanner includes the dynamic tracking error of the servo axes as part of its trajectory and corrects it in real time. The result is that the user receives dynamic tracking performance at scanner level over the entire part, regardless of the combined movement. At the same time, this allows the servo tables to be moved faster and more aggressively without compromising the overall accuracy and quality of the finished part.
One control platform for all applications and systems
The latest release of Automation1 is installed on all positioning solutions and systems at the Aerotech stand. The motion control platform functions as a complete machine controller with all components and therefore offers much more than just “motion control”. Equipped with a new software-based motion controller, it can be used to directly control servo and stepper motors, galvo scan heads, piezoelectric actuators and various other devices. The individual drive modules are connected via the HyperWire bus, currently the most powerful communication bus in the motion control industry.
In particular, the functional enhancements in the course of the new release will be presented. For example, the machine setup, data visualisation and the Homing help module have been significantly improved once again. Thanks to the API support of Python API, all Python help files of the controller are now also available.
“We would be delighted to convince trade visitors of Automation1, an innovative motion control platform in which we have closely coupled the process control with the
motion control,” explains Simon Smith. “This enables even faster movement and settling times, better position stability and increased contour accuracy.”
Six degrees of freedom solution with outstanding load-bearing capacity One of the applications on the stand that will be controlled with Automation1 is the HEX150 hexapod, as Norbert Ludwig explains: “Using the HEX150 as an example, we will be demonstrating the significantly better minimal incremental movement paired with greater linear travel, all on a compact yet rigid platform.”
The miniature hexapod is ideal for space-constrained applications with multiple DOFs (degrees of freedom). Precise translation in the X, Y and Z directions and rotation around each of these axes ensure fine positioning resolution. The positioning experts see applications, for example, in the alignment, assembly and connection technology of photonics components, optical inspection and alignment, optical wafer probing, sensor tests in aerospace and satellites as well as in sample alignment for synchrotron and beamline applications. As the proprietary simulation software “HexGen Hexapod” is integrated into the Automation1 control platform, control and programming with virtual pivot point adjustment and integration into complex applications and complete systems are simplified.
((Info 1))
Aerotech’s IFOV on YouTube: https://www.youtube.com/watch?v=wDRE9kNQGFw ((Info 2))
Infinite Field of View (IFOV) synchronises linear or rotating servo axes with laser scanners.
Design features:
- Easy-to-use set-up parameters and effortless execution for each profile
- Simultaneous trajectory generation in real time from a controller
- Automated dynamic error correction of servo table tracking by the scanner
- Supports advanced laser control functions such as position-synchronised output and analogue vector tracking
- Optimisation of the execution sequence for combined motion paths with the CADFusion package from Aerotech
- Designed for use with Aerotech AGV galvo scanners; compatible with third- party XY2-100 controlled scanners
((Pictures)) (all pictures: source Aerotech)
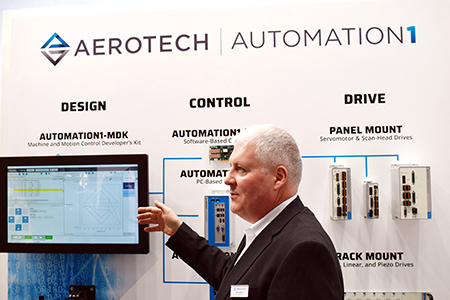
Image1: Simon Smith, European Director at Aerotech, on the upcoming trade fair: “Optatec, which takes place every two years, is a real industry highlight and the ideal stage for us to present our latest applications and manufacturing systems to a broad specialist audience. With IFOV and Automation1, we also have two real trade fair highlights up our sleeve”
Fig. 2-4: Aerotech IFOV Caption: Aerotech’s Infinite Field of View (IFOV) synchronises linear or rotary servo axes with laser scanners. Errors are eliminated and throughput rates are increased.
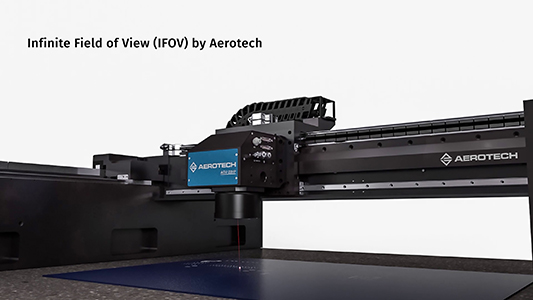
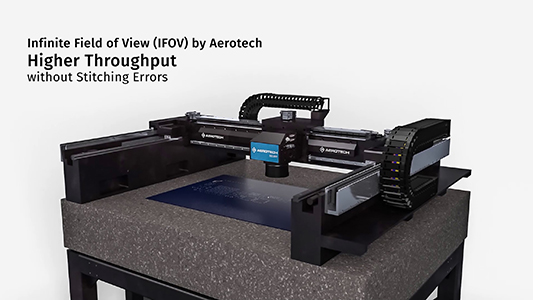
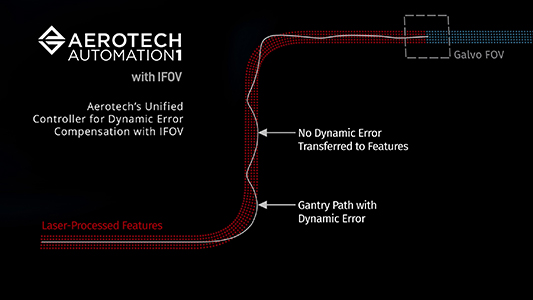
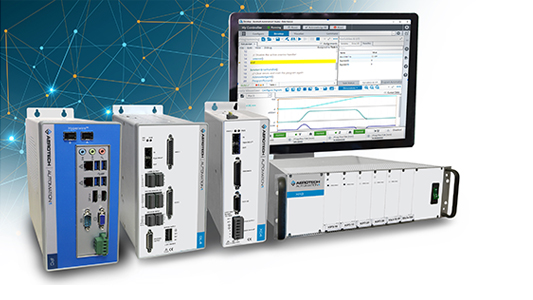
Image5: Automation1 Caption: Aerotech is presenting the latest release of the user-friendly Automation1 motion control platform at the trade fair, including Python Api and MachineApp.
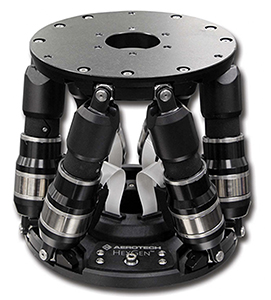
Picture6: Hex150 Caption: HEX150 from Aerotech with a high load capacity of up to 7.5 kg: Fast settling times with a travel range of up to 55 mm linear and 50 degrees of rotation ensure high throughput with repeat accuracies of less than 2 μm and a blocking force of up to 100 N.