It’s critical to preserve efficiency while guaranteeing the best quality in the fast-paced world of electronics manufacturing. High-Quality Design for Manufacturability, or HQDFM, is an approach that is essential to accomplishing these objectives. It maximizes product design to lower expenses, streamline production procedures, and enhance product quality. In this article, we explore the fundamental uses and advantages of HQDFM in contemporary manufacturing, emphasizing the contributions of pioneers in the field like NextPCB.
HQDFM: What is it?Â
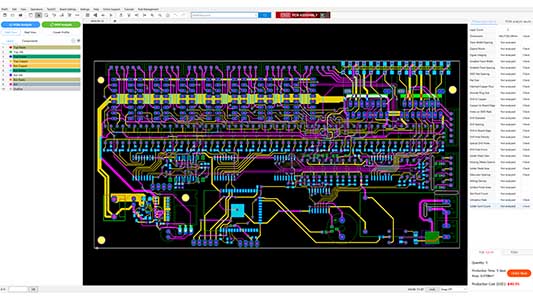
In the fields of manufacturing and design engineering, HQDFM is a cutting-edge methodology. It combines improved quality assurance procedures with the fundamentals of traditional Design for Manufacturability (DFM) to produce products that are not only simple to make but also perform and depend on high standards. By addressing possible manufacturing concerns early in the design process, this methodology guarantees more seamless production runs and higher-quality final products.
Principal Activities of HQDFM
- Â Design Optimization:
- Simplifying product designs is the goal of HQDFM. This is achieved by utilizing standard parts whenever feasible and minimizing the number of components. This simplicity lowers the possibility of production errors and shortens the assembly time.
- Standardization: Manufacturers can improve product consistency and quality by streamlining manufacturing and lowering variability through the standardization of parts and procedures.
- Selection of Materials:
- Sturdiness: Selecting the appropriate materials is essential to the product’s durability and functionality. HQDFM places a strong emphasis on choosing materials that can endure manufacturing processes and environmental conditions in addition to fulfilling functional requirements.
- Cost-Efficiency: Juggling quality and cost is a crucial component of HQDFM. The process promotes the use of affordable materials without sacrificing the product’s integrity.
- Processes Engineering:
- Production Methods: HQDFM entails evaluating and choosing the most productive production methods. This involves figuring out the most efficient ways to cut costs and save time while cutting, connecting, and assembling parts.
- Automation: A key component of HQDFM is the utilization of automation. Automated procedures can significantly improve production uniformity and efficiency since they are less likely to include human error.
- Testing and Inspection for Quality Control:
- The HQDFM method has strict processes for testing and inspection. This guarantees that, before being delivered to the client, every product satisfies the necessary quality requirements.
- Feedback loops: The design team must receive ongoing input from the factory floor. To rapidly address any difficulties and incorporate changes into future designs, HQDFM sets up robust feedback systems.
- Cost Management:
- Waste Reduction: HQDFM helps cut down on wasteful steps in the manufacturing process and eliminate material waste by optimizing designs and processes. This results in cost savings.
- Effective Use of Resources: HQDFM is known for its effective use of resources. This entails making the best use of machinery, people, and supplies to produce goods at a reasonable cost without compromising quality.
NextPCB and HQDFM
NextPCB is a leader in the PCB manufacturing industry, exemplifying the principles of HQDFM. By integrating HQDFM methodologies into their processes, NextPCB ensures that every PCB and PCBA they produce meets the highest standards of quality and manufacturability. Here’s how NextPCB applies HQDFM:
- Advanced Design Tools: NextPCB utilizes state-of-the-art design tools that incorporate HQDFM principles, allowing for the creation of optimized, manufacturable designs from the outset.
- Material Excellence: NextPCB carefully selects materials that provide the best balance of durability and cost-effectiveness, ensuring reliable performance in all their products.
- Efficient Processes: NextPCB leverages advanced manufacturing techniques and automation to streamline production, reduce errors, and maintain high-quality standards.
- Comprehensive Testing: Rigorous inspection and testing protocols at NextPCB ensure that every product meets exacting quality standards before it is delivered to customers.
- Continuous Improvement: Feedback loops within NextPCB’s processes enable continuous improvement, addressing any issues promptly and refining designs for future products.
Conclusion
HQDFM represents a comprehensive approach to manufacturing that integrates high-quality design principles with practical manufacturing strategies. By focusing on design optimization, material selection, process engineering, quality control, and cost management, HQDFM helps manufacturers produce superior products efficiently and cost-effectively. Companies like NextPCB are at the forefront of implementing HQDFM, ensuring that their products meet the highest standards of excellence. As the manufacturing industry continues to evolve, methodologies like HQDFM, championed by leaders like NextPCB, will be essential in meeting the demands of quality, speed, and cost-efficiency in modern production environments.