Abstract
This power management tip briefly explains a buck-boost topology and how releasing new regulators allows for Silent Switcher® technology to be used. Combining a buck-boost topology and Silent Switcher technology brings very low EMI at the highest power conversion efficiency.
Introduction
In many applications, voltages require upward and downward conversion. For example, if an input voltage range of 6 V to 24 V is available and 12 V is to be generated from it. Classical wide-range power supplies must be capable of such voltage conversions.
Different voltage conversion architectures are capable of voltage conversion upward and downward. These are transformer-based topologies such as fly- back regulators, single-ended primary inductor converter (SEPIC) topology, and a 4-switch buck-boost topology.
A 4-switch buck-boost is a very elegant architecture. Four switches are required here, but only one inductor is needed. Figure 1 shows the circuit topology. The coil is always controlled by the four switches in such a way that results in a buck switching regulator converting downwards or an upward-converting boost switching regulator. The conversion efficiency is high and the application of this type of circuit is quite simple.
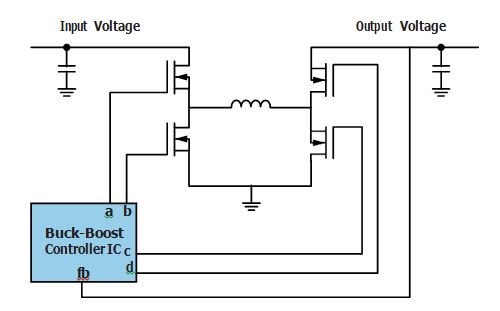
A switch-mode buck-boost converter works with a certain switching frequency and generates pulsed currents on internal traces of the voltage converter. These are located either on the input side in buck mode when the input voltage is higher than the desired output voltage, or on the output side in boost mode when the input voltage is lower than the desired output voltage. These pulsed currents cause a pulsed magnetic field, thus causing electromagnetic interference (EMI).
Silent Switcher technology has been available to design switch-mode power converters with very good electromagnetic compatibility (EMC) behavior. This technique divides the pulsed currents into two conduction paths, each with a high level of symmetry. This halves the amplitude of the pulsed currents and the symmetry largely cancels out the magnetic fields generated. Figure 2 shows the application of this technique to buck-boost controllers. Red shows the paths of the pulsed currents, whose magnetic fields cancel each other out by a symmetri- cal arrangement.
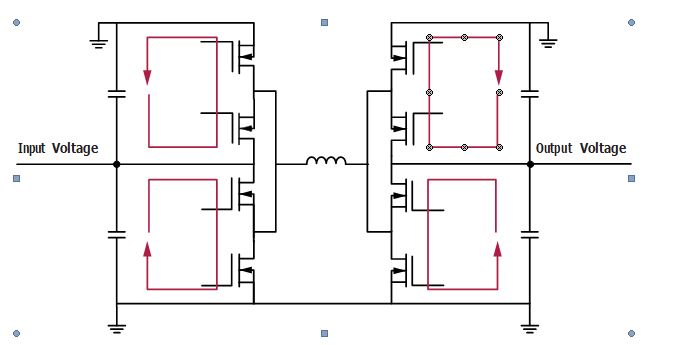
Figure 2. A version of Silent Switcher technology that cancels out magnetic fields of the pulsed current paths.
Figure 2 shows a total of eight switching transistors. A buck-boost circuit based on Silent Switcher technology requires only four switches, just like a conventional buck-boost topology. The additional switches in Figure 2 are drawn to make the symmetrically pulsed current paths recognizable.
With the combination of a buck-boost regulator and Silent Switcher technology, it is now possible to develop combined up and downconverters with very good EMC behavior. For the best EMC behavior, there are regulators with integrated decoupling capacitors, which are referred to as Silent Switcher 2 regulators. These capacitors from Figure 2 are already integrated into devices such as the LT8350S together with the integrated circuit. This reduces the parasitic effects in the paths of the pulsed currents and thus reduces radiated emissions even further compared to devices with external decoupling capacitors. An available version with external coupling capacitors is the LT8350.
Figure 3 shows a circuit with an LT8350S buck-boost switching regulator. This device can carry up to 6 A switch current and has an input voltage range of 3 V to 40 V. To reduce the generated EMI even further, it is optionally possible to use spread spectrum frequency modulation (SSFM). The circuit in Figure 3 shows the LTspice® simulation model with external circuitry, which is available free of charge.
Conclusion
Buck-boost switching regulators are suitable for voltage converter circuits that must convert voltages up and down. New integrated circuits from Analog Devices, such as the LT8350S, allow developers to execute this topology using Silent Switcher technology to design a switch-mode voltage converter with a very high EMC.
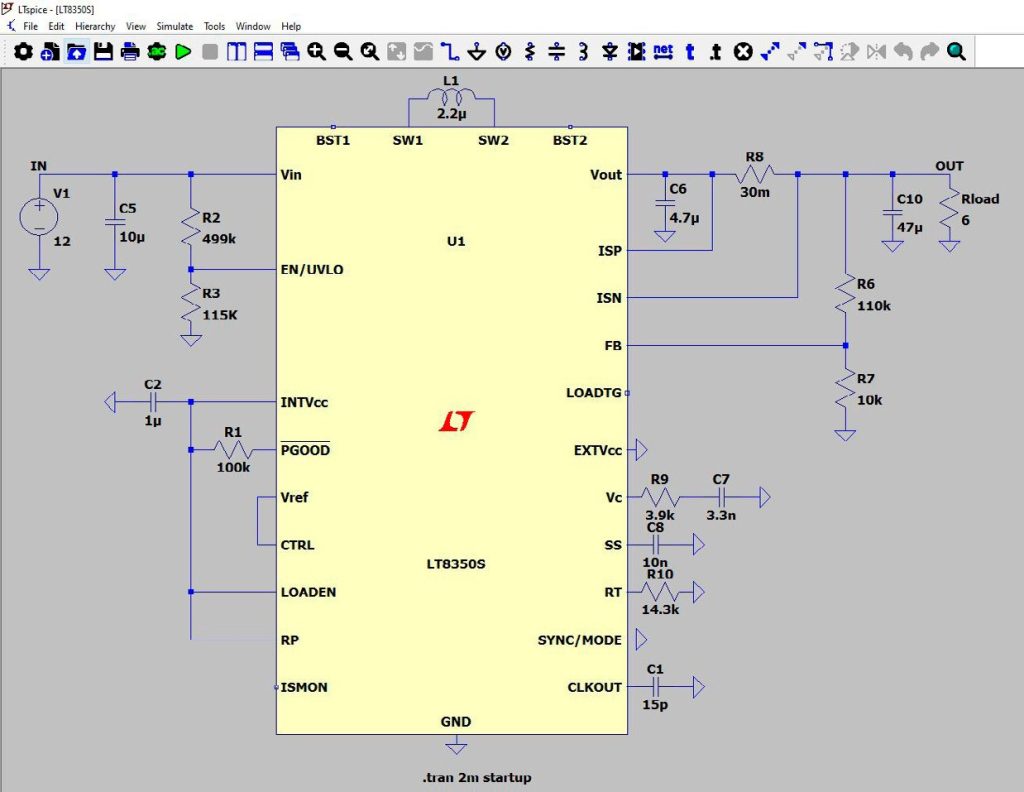
About the Author
Frederik Dostal is a power management expert with more than 20 years of experience in this industry. After his studies of microelectronics at the University of Erlangen, Germany, he joined National Semiconductor in 2001, where he worked as a field applications engineer, gaining experience in implementing power management solutions in customer projects. During his time at National, he also spent four years in Phoenix, Arizona (U.S.A.), working on switch-mode power supplies as an applications engineer. In 2009, he joined Analog Devices, where he has since held a variety of posi- tions working for the product line and European technical support, and currently brings his broad design and application knowledge as a power management expert. Frederik works in the ADI office in Munich, Germany.