~ Common product design challenges solved by custom ICs ~
Every product starts with a vision that design engineers are tasked with turning into reality. However, this process is far from straightforward, as products today must meet increasingly complex performance standards to keep up with market demand. Here, Ross Turnbull, Director of Business Development and Product Engineering at ASIC design and supply specialist Swindon Silicon Systems, explores how ASICs could address four common product design challenges.
In today’s rapidly-evolving and competitive market, design engineers face mounting challenges in developing products that stay ahead of the curve. Modern products are expected to deliver exceptional performance while adhering to strict requirements for size, power efficiency and reliability — all while meeting tight deadlines and budget constraints.
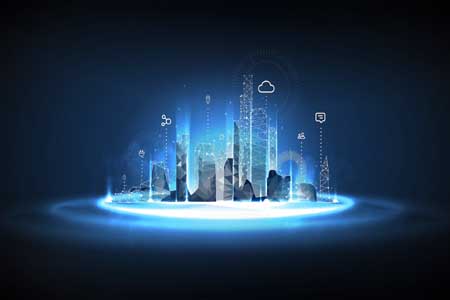
As the demand for advanced, specialised designs grows, the limitations of generic, off-the-shelf components are becoming increasingly apparent. To illustrate the benefits of a more tailored approach, it’s first helpful to examine some of the most common product design challenges.
Performance bottlenecks
Design engineers face significant challenges in ensuring seamless performance, particularly in high-performance applications such as advanced automotive systems and Internet of Things (IoT) devices. These applications require fast, reliable data processing and general-purpose components often lack the speed and throughput to meet these demands.
For example, field-programmable gate arrays (FPGAs) are valued for their flexibility, as they can be reprogrammed for a variety of tasks. However, this adaptability comes at a cost to efficiency. Since FPGAs are not optimised for specific tasks, they can struggle to deliver at the speed necessary for high-throughput processing. This is particularly problematic for time-sensitive applications like autonomous vehicles, where delays in processing sensor data can slow decision-making, compromising safety and system performance.
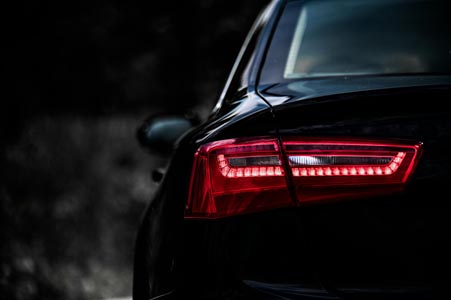
Size constraints
Another issue in the product development process is size, driven by the growing demand for sleek, lightweight and high-performing devices. With this comes the challenge of fitting more functionality into increasingly limited space.
More compact designs also pose thermal management challenges. As products shrink, it becomes increasingly difficult to dissipate heat efficiently. This results in components operating at higher temperatures, which can degrade performance, reduce lifespan and even cause system failures.
Another challenge lies in finding off-the-shelf integrated circuits (ICs) that meet the precise requirements of small-scale designs. Standard components, designed for general applications rather than tailored to these designs, often can’t deliver the required performance in such small systems. This forces engineers to compromise on performance, size or efficiency, as it can be challenging to find general-purpose components with all the desired features.
Power limitations
Power usage is also a key consideration in product design, particularly in applications where energy efficiency is crucial. However, compact designs come with inherent power limitations due to the reduced space available for batteries or power storage. In these smaller systems, optimising power consumption is vital, demanding a delicate balance between performance and energy efficiency.
For devices requiring continuous operation without frequent recharging, this challenge is even more pronounced. For instance, remote monitoring sensors in hazardous or isolated locations must operate reliably over extended periods with minimal maintenance, often under harsh environmental conditions. Minimising power consumption without compromising performance is essential to extend battery life. However, using off-the-shelf components can lead to unnecessary power consumption, as they are not tailored to meet the unique energy efficiency requirements of such devices.
Complex signal processing
Signal conditioning and processing are critical in modern electronic devices, which require raw analogue signals to be converted to digital data. However, this conversion can introduce latency issues that can delay system performance and even lead to failure. Additionally, signal conditioning and processing can be power-intensive, adding to the system’s energy demands.
It’s also crucial for chip components to perform accurate signal conditioning. Any errors in this process can distort the data, leading to inaccurate readings and disrupting operations. For instance, in industrial monitoring systems, even slight data distortions can lead to equipment malfunction or downtime, which can result in costly repairs and production delays. With the increasing complexity of data and the demand for smaller, more efficient systems, managing these signal processing tasks has become very difficult for off-the-shelf components.
How ASICs can help
To overcome these challenges, engineers need solutions that offer the precision, speed and efficiency required for high-performance systems. This is where ASICs come into play. Unlike general-purpose components, ASICs are custom-designed to meet the unique demands of specific applications, allowing every aspect of system performance to be optimised, from functionality to power consumption.
Mixed-signal ASICs are particularly beneficial in modern designs. These chips combine both analogue and digital functions in a single integrated solution, allowing for a more compact design by eliminating the need for multiple components. By integrating functions such as data processing, signal conditioning and communication into one chip, mixed-signal ASICs reduce latency, enhance data throughput and minimise power consumption. As well as simplifying system architecture, this also improves reliability, as fewer components reduce the risk of failure.
Swindon Silicon Systems specialises in creating high-performance, low-power ASIC solutions for industrial and automotive applications. These highly specialised ASICs can address performance bottlenecks, reduce power consumption and enable seamless signal processing even in compact designs, providing engineers with a significant advantage in developing next-generation products.
As technology advances, design engineers are required to balance increasingly demanding performance requirements with stringent power and size constraints. Custom ASICs offer a tailored solution to these demands by providing a level of optimisation that off-the-shelf components simply cannot match. With the ability to adapt to meet both current and future design needs, ASICs empower engineers to create cutting-edge products that stand out in competitive markets.
To find out more about the comprehensive ASIC design and supply services available from Swindon Silicon Systems, please get in touch with our experienced team.