The design of complex, high-power DC-to-DC converter architectures poses some challenges to engineers developing aerospace and military-grade power systems. DC-DC converters must comply with multiple standards and stringent requirements in terms of input voltage, EMI (electromagnetic interference) environmental conditions, and thermal management.
A modular approach can significantly simplify the design process, enabling engineers to design complex power conversion systems using COTS and SWaP-C optimized building blocks. Engineers can meet multiple industry standards and power requirements while optimizing their power architectures according to new industry standards such as the Sensor Open System Architecture (SOSA).
This article looks at how a flexible modular power architecture can help address these challenges.
Modular power solutions
Whereas a centralized power solution tends to be a single unit that provides multiple outputs, a modular approach offers the same (or better) performance through a combination of modules. The structure of each modular solution will vary according to the application’s needs. Typically, it will include several DC-DC converters that change a common bus voltage to meet the needs of the load(s).
Other modules may be included to provide an auxiliary voltage rail alongside EMI filters, limiters, and hold-up modules. This way, the output voltage remains present when there is a ‘dip’ on the input, for example, when cranking a vehicle engine.
Depending on the available supply type (AC or DC voltage), there may be an AC-DC front-end power supply including power factor correction to create a voltage rail to power all the modules in the system.
The modular approach offers significant flexibility to meet non-standard requirements without involving the cost and complexity of a custom design. As it typically uses pre-qualified modules as building blocks, challenges such as EMI are already quantified, and necessary approvals are already in place.
Military/avionic applications
For all power solutions in military/avionic applications, the most common power source is a pre-defined bus that will deliver either 24V DC or 28V DC. This applies to both airborne and ground-borne applications.
Various standards exist covering power systems within military/avionic applications, primarily to sustain input voltage excursions (including transients, spikes, dips due to engine cranking, or power source commutation and shut down).
Airbone Applications
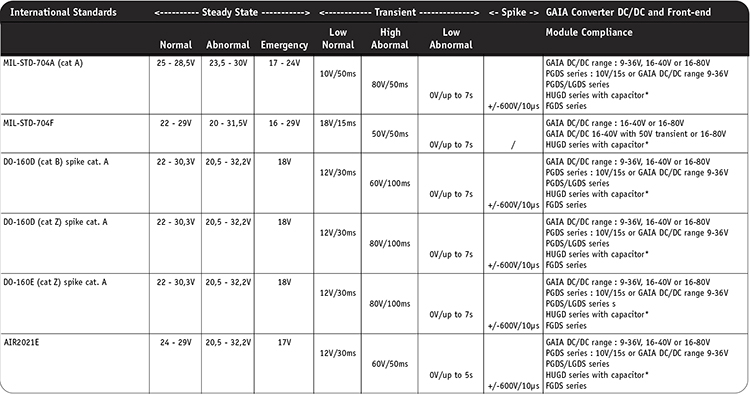
Groundbone Applications
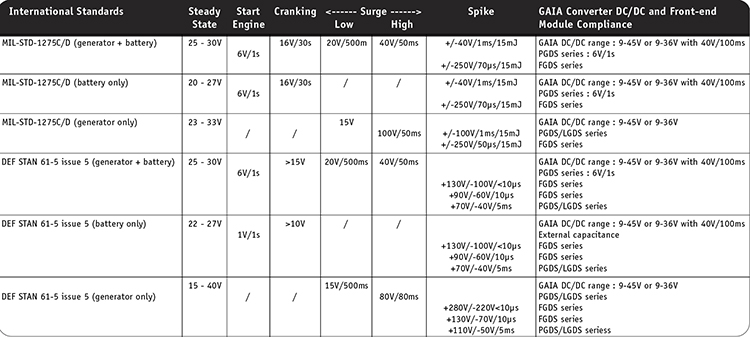
While the nominal voltages available within an aircraft or vehicle are well defined, the nature of military applications means that the system design must allow for fluctuations. Wide input range DC-DC converters can cope with either a 24V DC or 28V DC input and meet the excursions in airborne applications due to abnormal or emergency operating conditions. For vehicular ground-borne applications, the voltage deviations are most commonly due to engine starting or cranking or power source commutation. Again, using a wide input range DC-DC module will address this issue.
To meet other requirements, other types of modules can be added to the solution. For example, transients are addressed by GAIA’s LGDS series voltage limiter modules, while EMI filter modules (FGDS series) offer compliance to EMI emission standards
The system should also continue to deliver power for a brief (defined) period in the absence of any bus power. This ‘hold-up’ time is often addressed with a bulk capacitor connected across the bus at the input to the DC-DC converter modules. However, there are two issues with this approach. Firstly, the charged voltage of the capacitor being the nominal bus voltage, the size of capacitor will be extremely large. Secondly, a so large capacitor will require external circuitry to limit inrush current.
A hold-up module (such as GAIA’s HUGD-300) can help address these challenges. This module charges the capacitor at a higher voltage (usually in the range of 31V DC to 80V DC) and manages any inrush current associated with the bulk capacitor. As the energy stored increases by the square of the voltage, this approach results in a much lower value of the bulk capacitor, which is also physically smaller and more affordable.
Electrical noise
Due to the enhanced efficiency and smaller size, almost all DC-DC converter modules are switching devices; they switch the DC input to create an AC waveform that is then regulated to give the output DC voltage. As mentioned, this approach enhances size and efficiency. However, it also creates the potential for electrical noise, which can have a detrimental effect on other system components if not properly controlled. For this reason, standards including MIL-STD-461 and D0-160 define the maximum amount of permissible noise, both conducted and radiated.
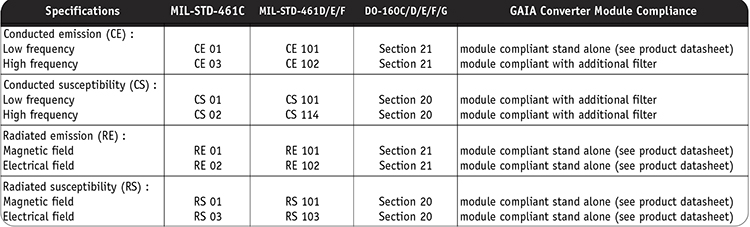
Many converters contain some form of inbuilt noise suppression for conducted noise and a grounded metal case significantly diminishes radiated noise. For more stringent standards, external filter modules (like GAIA’s FGDS series) can be added to the input of DC-DC converters to reduce noise further.
Many of GAIA’s DC converters are equipped with a synchronization pin that allows the switching frequency of the module to be ‘steered’ away from frequencies to which the system may be sensitive. Additionally, in multi-module systems, the switching frequencies of each module can be aligned exactly by connecting the synchronization pins. In doing this, the designer can eliminate the low frequency ‘beat’ noise that can be generated by small differences in the switching frequency of individual modules.
Operating environment
Military/avionic systems may be deployed in a variety of locations and subjected to different and challenging environmental conditions, including temperature extremes, humidity, shocks, and vibrations. A range of standards defines the requirements for the operating environment, along with outlining the tests to undertake to ensure that a module is compliant.
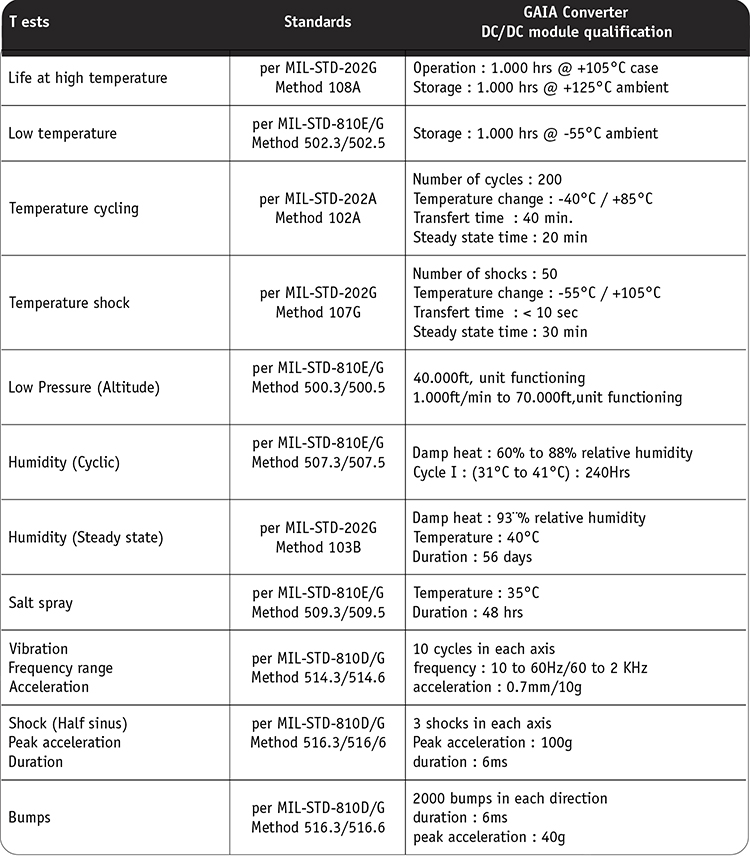
In the case of a custom power solution from discrete components, these tests would have to be passed after the design is complete. This process would involve a significant amount of time, cost, and design risk and probably require some design changes. Also, any significant design changes or upgrades would be subject to re-test and re-certification – again with time, cost and risk.
However, the modular approach uses pre-qualified modules that have already demonstrated their ability to meet the relevant standards, eliminating much of the design risk and dramatically simplifying the approval process.
Thermal management
Heat is always an issue for any power system, no matter how efficiently it can operate. This is especially true for any system used in a confined and/or enclosed space, as in military/avionic applications. Any thermal design must include some design margin to ensure the reliability of the modules.
GAIA converter modules are designed for a maximum case or baseplate temperature (depending upon the style) of 105°C.
In almost all cases, thermal management will be required, including forced air cooling using a fan, thicker and larger metallization on the circuit board, some form of heatsinking – or a combination of these techniques. In many cases, a preferred method is a thermally conductive heatsink that is in contact with the metal case/baseplate of the power module.
Conclusion
Designing power solutions for military/avionic applications can be challenging due to the operating environment and the stringent standards. In many cases, taking a modular approach using off-the-shelf, pre-approved modules is the best approach as it reduces design time and risk.
While many of the applicable standards have been in use for some time, there are updates made to address new applications or incorporate new technology. Designers must ensure that the modules used in their designs are compliant with the latest versions of all standards to ensure design longevity. Additionally, other organizations like the Sensor Open Standards Architecture Consortium (SOSA Consortium) are actively enabling governments and industry to develop open standards and best practices that apply to the military use of sensing devices.