Electronics Era: Explain in brief about Universal Robots?
Sougandh K.M.: Revolutionising the automation industry since 2005, Universal Robots (UR) is now the Danish pioneer of human-robot collaboration. Universal Robots aims to empower change in the way work is done using its leading-edge robotics platform. Since introducing the world’s first commercially viable collaborative robot (cobot) in 2008, UR has developed a product portfolio including the UR3e, UR5e, UR10e, UR16e and UR20. These cobots reflect a range of reaches and payloads, and are designed to work alongside humans without any safety fence or enclosing (upon risk assessment).
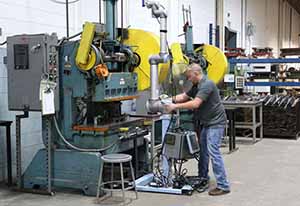
UR has more than 1000 employees worldwide and a comprehensive network of over 800 distributors and certified system integrators located in over 60 countries. The company has sold more than 50000 cobots globally. Each model is supported by a wide selection of end-effectors, software, accessories and application kits in the UR+ ecosystem. This allows the cobots to be used across a wide range of industries and means that they can be redeployed across diverse tasks.
Electronics Era: Where do you find automation to be the most beneficial in the packaging process?
Sougandh K.M.: For manufacturers, automation offers a variety of advantages. The biggest concern for any organisation is lowering operating costs and raising productivity. Automation has streamlined and sped up the packaging process significantly. The benefits of automation in the packaging process have been established:
• Productivity: Typically, packaging processes can be repetitive and dull. Human errors may occur when employees work on such monotonous tasks after a prolonged period of time. However, automated solutions or robots can take on these repetitive tasks without breaks, ensuring that processes are conducted with accuracy and precision.
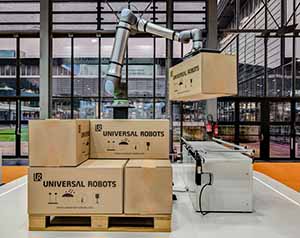
• Protecting worker’s safety and well-being: Packaging processes involve some of the least ergonomic tasks in the supply chain, accounting for a significant number of repetitive strain and musculoskeletal disorders among workers. Cobots are relieving human employees from lifting heavy loads and bending to pick up or wrap goods that carry the risk of injury.
Electronics Era: What are some of the biggest misconceptions when it comes to automating packaging lines? How are universal Robots changing this?
Sougandh K.M.: When it comes to automation, there are many misconceptions regarding robots, for instance:
• Higher costs of automation: Automating packaging lines are often seen as an expensive process and require professional engineers to operate and maintain the traditional industrial robots. However, cobots are easy to program and even workers with no robotic or programming background can operate a cobot. Besides, cobots unlock significant gains in productivity and quality, as well as cost savings and ROI.
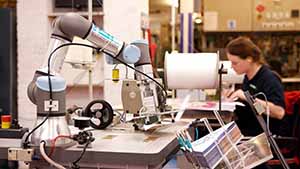
• Robots are unsafe for workers: Traditional industrial robots are pictured as the large and bulky machinery that could pose a danger to human employees. However, quite the opposite is true for cobots. Cobots are designed to work alongside humans, posing less risk to employees.
• Infrastructural changes: The deployment of conventional robots may require infrastructure upgrades and a large amount of area due to their vast size. However, UR cobots are compact and have smaller footprints. They can also be mounted to the ceiling, hence, limited space with negligible infrastructural changes are required.
Electronics Era: What are some of the latest technologies being incorporated in the automation process nowadays?
Sougandh K.M.: The automation process has undergone a complete transformation over the past decade due to technological advancements. The automation process has changed significantly, going from massive, cumbersome robots to small, simple cobots. Here are a few examples of the cutting-edge technology whose adoption has revolutionised the automated process:
• Artificial Intelligence: Industry experts are utilising AI to foresee issues with their equipment, enabling them to better focus on preventative maintenance and repair. Artificial intelligence (AI) may also be used to try out potential solutions and make an educated decision at very cheap costs and without running the risk of endangering equipment or employees.
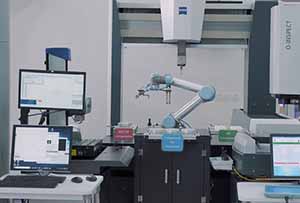
• Industrial Internet of Things: The Industrial Internet of Things (IIoT) is the term used to describe how connected equipment are, and it is growing more and more important across all sectors. With the help of improved sensors and interconnects, objects may now communicate with people remotely.
Electronics Era: Being the emergence of Industry 5.0 it opens a new world where collaboration between robots and people is perfectly synchronized. Could you help us understand how it will transform the manufacturing sector?
Sougandh K.M.: The connection between humans and machines is highly valued in the “Industry 5.0” manufacturing concept. Technology was created exclusively with humans in mind and not to take their place. Adopting Industry 5.0 has several benefits for manufacturers:
• Manufacturers may boost their competitiveness by lowering manufacturing costs.
• By skilling and upskilling employees, manufacturers are put at the centre of the industry, giving them more leverage.
• Collaborative automation gives businesses a competitive edge by increasing and maintaining the quality of their products, increasing output, and lowering total costs.
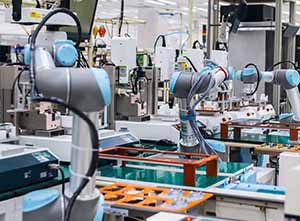
• Because cobots are versatile, easily programmable, and safe, expensive, space-guzzling safety caging can almost always be done away with. Robotic capabilities can then move out of closed factories and limited-access spaces, to work side-by-side with us humans. Robotic capabilities become a personal tool that members of any workforce can use to apply their distinctive creative skills more effectively, to provide greater human value.
• This then leaves human employees free to apply their intangible skills and difficult-to-program creativity to more complex projects – or to notch up a considerable boost in productivity for their existing craft or skill.
Electronics Era: Now Indian Industry is becoming futuristic and competing with the global manufacturing companies. According to you, how are cobots being the key-changer for Indian SMBs?
Sougandh K.M.: Indian SMBs are labour-intensive and have a great scope for expansion. As cobots are flexible, economical and versatile, the deployment of cobots can save costs for them. Typically, high capital investments are required to deploy a traditional industrial robot. However, cobots can be deployed to benefit all aspects of businesses regardless of their size. Now, cobots are no longer an option only applicable to larger organisations. They give SMEs the opportunity to grow in measured steps so that they can maintain competitiveness in a global landscape without taking on undesirable risks.
Thanks to the variety of benefits that cobots offer, the new approach to automation through cobots has been advantageous for manufacturers. Additionally, the introduction of Industry 4.0 and numerous government-led programmes have been crucial in the adoption of cobots throughout the nation.
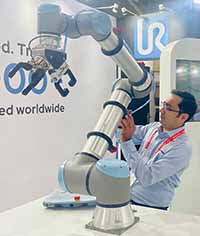
Electronics Era: What are the contributions that cobots made in achieving the sustainability goals?
Sougandh K.M.: Just like multiple other benefits, cobots are beneficial in achieving the sustainability goals:
• Cobots are an energy-efficient solution: As cobots use far less energy than typical robots, the electricity used are significantly reduce, emitting less carbon dioxide. Additionally, cobots may be monitored remotely using any smartphone, tablet, or laptop, giving the manufacturer the option of remote access. Manufacturers may remotely programme their cobot(s) via remote access technologies, saving on travelling expenses and decreasing the environmental effect of the automation deployment.
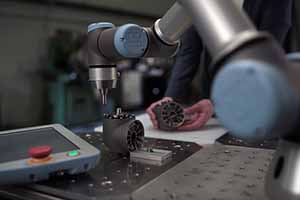
• Cobots have a smaller footprint: Traditional robots require greater deployment areas and infrastructure modifications due to their enormous, bulky size. Upon risk assessment, the majority of cobots do not need safety guarding, making it simple to transport them between applications and avoiding expensive facility redesigns. Cobots are lightweight and have a modest footprint.
• Cobots decrease waste: Manufacturing defects and discarded raw materials are not only costly to companies, they become waste which impacts the environment. Cobot deployment reduces mistakes caused by human errors, resulting in the reduction of wastage.
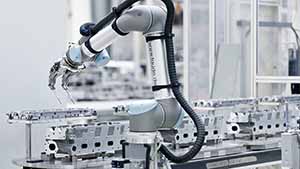
Electronics Era: How cobots help in enhancing workplace experiences?
Sougandh K.M.: Collaborative automation has changed how people operate in the manufacturing industry. Cobots have freed human workers from labour-intensive, tiresome, and hazardous duties. Cobots are designed to carry out monotonous activities while working safely near humans. Cobots relieve the workers from the tedious and time-consuming tasks so that they may concentrate on tasks that are more valuable.
Additionally, cobots contribute to greater employee satisfaction by relieving workers from the tiresome, repetitive labour and allowing them to concentrate on more creative pursuits. As a result, this increases job satisfaction and employee morale. Besides, as nations continue to develop the next generation of talent, the incorporation of cobots is attracting and retaining young engineers.