By Carrie Gan, Mouser Electronics
When the Nissan Leaf made its debut in 2011, it was hailed as the world’s first truly mass-produced electric vehicle (EV)[1]. Since then, the EV market has expanded significantly despite its size, longstanding processes, and the usually elongated research and development cycle – all of which can slow down innovation. In the 10 years since the launch of Leaf, the market witnessed an incredible proliferation of fully electric vehicles, with over 450 different models on the market by 2021, with the compound annual growth rate (CAGR) for new models reaching an impressive 34% between 2015-2021[2].
Despite recent challenges for global markets, the passenger EV market continues to grow. However, it is a different picture, in the commercial sector, which includes larger and heavier vehicles used for transporting goods.. Studies show that commercial medium- and heavy-duty vehicles account for 40% of the emissions that come from road transportation, but they only make up 4% of the total road users[3]. This stark statistic underpins the need for technological development to support the evolution of commercial Large or Heavy Goods Vehicles (LGVs/HGVs) for a sustainable future.
In this article, we will explore the challenges faced by the commercial EV market and f the effective strategies to overcome the barriers.
Hurdles for the Adoption of Commercial EVs
In 2022, 14% of all new passenger vehicle sales were for electric models. In comparison, 1.2% of global sales were for electric trucks[4]. This can be attributed, to the varying levels of complexity in the vehicles.
HGVs are typically defined as vehicles weighing over 3,500kg. This category includes multiple sub-classes, such as articulated lorries, tankers, and trucks designed for a specific function, such as logging or concrete mixing. These vehicles are typically required to travel long distances, have two to six axles, and are frequently required to interface with larger machines – such as loading systems and trailers. In addition to these larger HGVs, smaller vans and specialised last-mile delivery solutions, like motorbikes, also play a vital role in modern distribution and haulage networks (Figure 1).
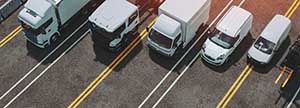
Figure 1: Examples of typical commercial vehicles. (Source: phaisarnwong2517/stock.adobe.com)
Compared to passenger cars, the electrification of HGVs can be expensive due to added design complexity because of the requirement to carry heavy loads, which requires large and powerful batteries to cope with the additional weight. Further challenges are introduced by the current limitations of battery technology and the added weight of the battery itself, impacting the total load capacity of the vehicle.
Support infrastructure is also an area where the hurdles are significant. A charging network to support electric trucks is exponentially more complex and expensive than one for passenger vehicles. Furthermore, charging stations for commercial vehicles need to be more powerful, raising additional safety and performance-related design challenges.
Progress in India
Efforts by the Ministry of Heavy Industries (MHI) to promote EVs in India have been ongoing. Although there are currently 12,146 charging stations, many of them are designed for passenger vehicles. Hence, there is a pressing need for rapid expansion of the charging network.[5] Mahendra Nath Pandey, the Minister of Heavy Industries in India, announced in 2023 that by 2030, the country’s nine major cities should have no less than 18,000 public charging stations. A separate estimate by the Confederation of Indian Industry suggests that India needs a minimum of 1.3 million charging stations by the decade’s end.
Navigating the Technical Challenges
At a basic level, the challenges faced by commercial and passenger vehicles are the same – limited range due to the weight of the vehicle. This is exacerbated by user expectations and the disparity between the energy density of traditional diesel-fuelled vehicles and those powered by electricity. Even though the powertrain for an EV is more efficient than a diesel-powered counterpart, where the thermal efficiency is around 40%[6], this does not counterbalance the increase in weight/energy output. As a case in point, diesel offers an energy density of approximately 12,500Wh/kg[7], in contrast to an average Li-ion cell with a density of approximately 300Wh/kg[8]. The increase in weight also adversely affects the vehicle’s range, leading to additional engineering considerations for suspension and tires.
Battery Swapping
China accounted for 85% of global sales, with around 52,000 electric medium- and heavy-duty trucks sold in 2022[9]. In China, there is also a concerted push to support the market with appropriate infrastructure, providing a potential roadmap for other countries on how to support the growing use of EVs.
A prime example of this is the growing trend of battery swapping in China, which is provided alongside the infrastructure for traditional charging stations. This strategy aims to address range anxiety, reduce charging times, and potentially lower battery costs for both commercial and passenger vehicles. The several factors that drive this unique approach, include:
Government Support
The Chinese government sees battery swapping as a way to accelerate EV adoption by overcoming charging time limitations, especially for commercial fleets like taxis and buses. The government even offers subsidies and pilot programs to promote the technology.
Standardization Efforts
Unlike the fragmented landscape in other regions, China is actively working on national standards for battery-swapping systems. This ensures compatibility across different manufacturers and promotes a robust ecosystem.
Strong Backing from Industry Leaders
Major Chinese automakers such as Nio and Geely and battery giants like CATL are heavily invested in battery-swapping solutions and are developing compatible vehicles and swapping stations to create a comprehensive network.
Battery swapping is a fully automated process and can be completed in as little as 3-5 minutes[10]. The battery pack is extracted by robotic arms, which is then replaced with a newly charged battery pack. The drained battery is then charged for use in another vehicle. This removal and replacement option provides a much faster alternative than leaving the battery pack in place and waiting for it to charge, providing commercial vehicles with a more cost-efficient way to keep vehicles on the road. In addition to speed and convenience, battery swapping has other benefits. By separating battery ownership from vehicle ownership, battery swapping allows for economies of scale, potentially lowering the upfront cost for the initial purchase of the vehicle. Swapping stations also offer the ability to manage battery health, providing a central point responsible for the maintenance of the batteries, potentially leading to extended battery lifespans and reducing overall battery waste.
The International Council on Clean Transportation (ICCT) reports that the initial assessments demonstrate the success of the infrastructure. However, the primary objective has been to aid the operation of electric trucks specifically designed for short-distance tasks in ports, mining areas, and urban logistics. These trucks typically have either a 141kWh or 282kWh lithium iron phosphate (LFP) battery and an average travel distance of under 100km.
There are still barriers that need to be addressed before battery swapping becomes a mainstream commercial practice. The primary obstacle is the lack of standardisation for battery packs. Cost is another barrier – according to the ICCT, setting up a battery-swapping station in China can cost approximately $1 million17. Despite these hurdles, China’s commitment to battery swapping is a significant development in the global EV landscape. Its success could influence other countries and potentially shape the future of EV infrastructure.
Fast Charging Networks
Governed by CharIN, a consortium established by prominent automotive authorities from around the globe, the Megawatt Charging System (MCS) is one possible solution to address long stop times. The MCS standard is recognized worldwide and aims to make safe and high-performing chargers the norm. The guidelines specify the need for a conductive plug to support 1250VDC and 3000A, vehicle-to-everything Ethernet communication, and standardised charging port positions on vehicles.[11]
, Truck manufacturer MAN estimates that using MCS for charging could be as fast as 10 minutes[12], which is a substantial advancement compared to current technology. Although MCS focuses primarily on commercial vehicles, it can also be customised for buses, aircraft, and other large EVs capable of charging above 1MW.12 Faster charging speeds can reduce the need for multiple charging stations at busy transport hubs, allowing trucks to spend more time on the road.
Solid State Batteries
Solid-state batteries substitute the separator and electrolyte with a solid ceramic or polymer substrate, as typically seen in a standard Li-ion cell.. The solid substrate allows the cathode to be effectively separated from the anode, which is usually composed of pure lithium. By incorporating a pure lithium anode and altering the structure, energy densities improve significantly, with theoretical levels reaching as high as 11kWh/Kg. However, a more realistic value of 1kWh/Kg is attainable in the near future. By exceeding current cell capabilities, solid-state batteries could maintain the same capacity while being 30% lighter.[13]
The enhanced energy density allows vehicle designers to achieve smaller sizes, higher payload capacity, or longer range. For many cost or performance-limited operations, this upgrade in performance could allow a switch to EVs.
Automotive analysts anticipate that large solid-state solutions will become commercially viable starting in 2025; these have evolved from small solid-state batteries, like the TDK CeraCharge™ Rechargeable Solid-State SMD Battery, that is currently on the market. Aligning with these projections, Toyota has recently unveiled its plans to manufacture vehicles incorporating solid-state batteries, beginning in 2025. These vehicles will have a range of 700km and can be fully charged in just 10–15 minutes.[14]
Conclusion
The transition to electric vehicles, especially in the passenger market, is an impressive step forward – both in terms of consumer perception and the technology that has allowed EVs to evolve since the Nissan Leaf. However, the slow acceptance of electric commercial vehicles highlights the urgent need for a focused effort to address the unique technical challenges in this market to close this gap, with the electronics sector playing a pivotal role.
High-performance and standardized electronic solutions, including breakthroughs in solid-state battery technology, the expansion of fast charging networks like the MCS, and exploring innovative ideas like battery swapping, pave a path to wider adoption of commercial EVs. With the support and collaboration between automotive manufacturers, electronics manufacturers, and policymakers, the automotive industry can unlock a future where EVs dominate the commercial landscape.
[1] https://www.nissan-global.com/EN/STORIES/RELEASES/nissan-leaf-10years/
[2] https://www.iea.org/reports/global-ev-outlook-2022/trends-in-electric-light-duty-vehicles
[3] https://www.theclimategroup.org/creating-market-medium-and-heavy-duty-zero-emission-vehicles
[4] https://www.iea.org/reports/global-ev-outlook-2023/trends-in-electric-heavy-duty-vehicles
[5] https://pib.gov.in/PressReleaseIframePage.aspx?PRID=2003003
[6] https://dieselfuelhq.com/why-do-trucks-and-buses-typically-use-diesel/
[7] https://energyeducation.ca/encyclopedia/Energy_density
[8] https://www.cei.washington.edu/research/energy-storage/lithium-ion-battery/
[9] https://www.iea.org/energy-system/transport/trucks-and-buses
[10] https://theicct.org/china-is-propelling-its-electric-truck-market-aug23/
[11] https://www.charin.global/technology/mcs/
[12] https://www.man.eu/uk/en/advice-and-offers/consulting/getting-started-with-e-mobility/charging-infrastructure/charging-infrastructure.html
[13] https://electronica.de/en/discover/industry-portal/detail/solid-state-battery-the-holy-grail-in-battery-research.html
[14] https://www.toyota.ie/company/news/2021/solid-state-batteries