Advances in technology and socio-economic factors are fuelling innovation and the adoption of agricultural robots.
Over the next half-century, the global population and, therefore, the demand for food will continue to rise. It is estimated that already 10% of the world’s population does not have enough food and by 2050, the demand for food will increase by 50% from today’s levels.
However, it is getting increasingly difficult to manage our agricultural lands and woodlands. The 2023 report by the Food and Agriculture Organisation (FAO) of the United Nations (UN) states that extreme weather events such as floods, droughts, and wildfires are becoming more frequent and severe, impacting agriculture and food security.
In the past three decades, the rising occurrence of natural disasters has led to a loss of approximately $3.8 trillion in crops and livestock production, equivalent to 5% of the world’s agricultural GDP.[1] These weather events, along with excessive farming practices, are causing severe environmental damage, including soil depletion, and according to the UN FAO, it is estimated that 90% of the Earth’s valuable topsoil could be at risk by 2050.
Reducing Risk and Increasing Yields
So how do we do more with less, while simultaneously mitigating the growing risks to plants and produce? The answer could be a new generation of agricultural robotics and automation, supported by the latest cutting-edge perception and analytic technologies.
These developments create opportunities for better land management methods, promoting sustainable agriculture and, in certain instances, revitalizing barren land for cultivation. For example, autonomous robotic irrigation systems can optimize water efficiency and crop yield. This automation allows for integrating intelligent wireless soil sensors for feedback and edge computational control, backed by cloud-based AI modelling to ensure accurate water delivery. Compared to traditional measures, automated and intelligent irrigation can better manage our use of resources and help to ensure that crops have what they need to grow.
Furthermore, robotics in agriculture can transform traditional farming practices by automating labour-intensive activities like seeding, weeding, and harvesting. Robots can work continuously, unlike humans, which boosts productivity during crucial farming seasons.
The combination of robotic systems, farm management software, and data analytics platforms enables the optimization of resource allocation, performance monitoring, and real-time data-driven decision-making. For often labour-strained farms, robotics can help to remove staffing concerns, therefore increasing yields and operational efficiency.
Component Progression
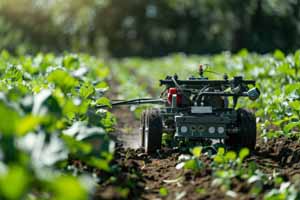
Studio/stock.adobe.com)
In terms of technology, the convergence of increasingly accurate positional sensors, more precise force sensors, and advanced actuators pave the way for the creation of robotic manipulators that exhibit the necessary level of gentleness to harvest even the most delicate crops.
AI-based image recognition is also playing a crucial role in advancing agricultural automation, facilitating the creation of sophisticated and more accurate autonomous farming machinery.
Automated Agriculture
Typical automated agricultural vehicles aim to mimic traditional farming machinery by incorporating booms or flexible arms that can be outfitted with different tools such as drills, plows, threshers, separators, cleaners, probes, sprayers, applicators, and other equipment, along with an increasing number of sensors.
However, in recent years, there has been a rise in the use of custom robotics alongside automated farming vehicles, providing a diverse range of solutions to enhance the capabilities of modern farms.
Drones
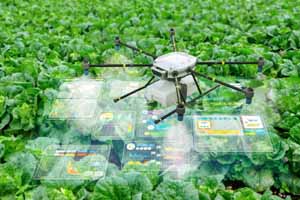
Compared to traditional machinery or human intervention, drones are also capable of quickly and accurately addressing problems on vast farmlands. By employing cameras and optical sensors, autonomous drones offer aerial imagery that aids in crop monitoring, pest identification, and disease detection, as well as targeted inventions such as fertilizer and pesticide spraying and fruit picking.
According to a report by Global Industry Analysts Inc., the global market for agricultural drones is expected to reach $5.7 billion by 2025. This growth is primarily due to the increasing demand for precision agriculture techniques.
Picking Machines
Robots designed for picking fruits and vegetables are a major advancement in automating agriculture. They provide a combination of accuracy, productivity, and scalability to contemporary farming practices. These autonomous machines are designed to handle the delicate task of harvesting crops, using advanced technologies such as machine vision and AI to drive ultra-precise robotics.
By determining the ripeness of fruits and vegetables, these robots can pick produce with minimal damage, leading to less waste and consistent quality. Key critical electronics enabling picking robots include high-resolution cameras, control electronics using AI or machine learning (ML) models to recognize and evaluate fruit ripeness, gentle robotic arms with soft grippers for handling the crop, and GPS systems for precise field navigation.
The integration of farming robots not only increases the speed and accuracy of harvesting but also addresses labour shortages and operational inefficiencies, making farms more productive and sustainable.
Weeders
Many agricultural machinery manufacturers now offer automated tractors with AI-powered vision systems and sprayers attached to their booms. AI can differentiate between crops and weeds, and accurately operate the sprayers to only target the weeds while leaving the crops unaffected.
Carbon Robotics has developed the LaserWeeder™, which utilizes computer vision and AI powered by Nvidia GPUs to detect crops and weeds accurately. Rather than using herbicide to spray them, it uses 150-watt carbon lasers to burn the weeds. The LaserWeeder comes in a commercial version that can be easily attached to a traditional tractor, and the company is also showcasing a fully autonomous variant of the product.
Enabling Technologies
Mouser Electronics stocks a wide range of cutting-edge technologies that are propelling the agricultural automation and robotics market, helping to unlock new applications and elevate yields while reducing resource use.
Intelligent Edge-Based Control
Relying on cloud-based intelligence or processing in agricultural robotics can be problematic due to the risk of communication failures. Constant cloud-based communication can impact the battery life of portable farming robots, and the lack of cellular coverage in expansive farming areas presents another significant challenge, with the cost of implementing local Wi-Fi® networks often being too substantial to consider.
Alternatively, edge-based AI or ML processing, by keeping intelligence onboard, enables agricultural robots to perform real-time analysis and decision-making without external network dependence, reducing power consumption and reliance on outdoor communication networks. Edge processing is proving a game-changer for tasks like obstacle detection, precision planting, and real-time crop health monitoring, helping to enhance efficiency and safety while operating with minimal delay.
Precise Sensing
The advancements in sensor technologies have paved the way for the development of a new generation of robotic and autonomous fruit pickers. Image sensors, like onsemi’s AR2020 HyperLux LP 20MP, offer high-resolution images with an extended dynamic range to ensure precise accuracy in machine vision applications, even in demanding outdoor conditions.
To balance performance and power consumption, the sensor also incorporates several intelligent features, including Wake-on-Motion (WOM) and subsampling modes, which effectively conserve power and minimize data usage.
With advancements in positional sensors, manipulators such as claws, suction cups, and scissors are now capable of collecting fruit from vines with great precision, without causing any damage. Murata Electronics provides a diverse selection of MEMS sensors, including the SCA3100-D07-1 accelerometer and SCC2230-D08-05 gyroscope.
These sensors are designed for positioning systems that require high sensitivity to inertial forces and pressure while remaining unaffected by other environmental factors. Constructed with single-crystal silicon and glass, Murata’s silicon capacitive sensors offer exceptional stability and temperature resilience. Moreover, their gyroscopes possess remarkable sensitivity and can detect even the slightest signals, such as the earth’s rotation.
Efficient Power Design
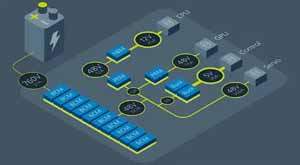
1/16th fixed ratio output. (Source: Vicor)
While certain agricultural robots prioritize low power for extended use without charging, larger agricultural systems still require high-power batteries operating at voltages above 400VDC.
Vicor is known for its expertise in supplying high-power components for battery-operated systems specifically designed for agricultural robotics. The BCM converter series is capable of converting high-voltage batteries to a safe 48V nominal voltage. Take the BCM4414 as an example, with its compact size of 111mm × 36mm × 9mm, it can deliver over 1,600W of power with an impressive efficiency of over 97%
The 48V output, which is isolated for safety, can be used to power separate lower-voltage rails for control, drive, and sensor systems by employing fixed-ratio or regulated point-of-load converters. The BCM4414 is ideal for agricultural automation designs as it promotes seamless integration due to its compact size, lightweight construction, built-in EMI filtering, and isolated design.
Conclusion
Progress throughout the electronics and software industries is helping to offer innovative solutions that enhance productivity, sustainability, and resource management. Despite the ongoing and significant global challenge of food production, we can confidently state that with the assistance of agricultural robotics, we will be well-positioned to address this challenge.
Furthermore, as underlying sensors, control, and communication components continue to advance, the solutions available will only evolve further, benefiting us all.