Sensors for industrial wearables
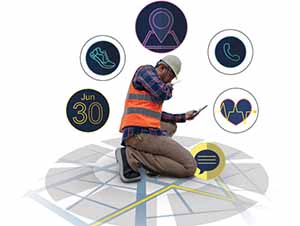
A safe and secure work environment is crucial for employees and employers. All industrial units, big or small, must incorporate safety in their work premises. Wearable technology allows industries to monitor and maintain the safety of employees on the shop floor. Sensors driven by the widespread use of IIoT and wireless technology allows increasing number of industrial devices or equipment incorporating features such as ultra-compact, high-accuracy, harsh media resistant, and power efficient solution. They are vital to the Industry 4.0 as they increase operational efficiency, optimise business processes, and reduce downtime. In this article, we’ll discuss the importance of industrial wearables, communication and localization techniques, and how they contribute to maintaining a safe work environment.
Why are wearables required?
Industrial wearables are commonly used in manufacturing environments to perform many tasks that improve occupational safety. It possesses the ability to monitor employees’ physiological factors, enhance operational efficiency, promote work environment, and improve workers’ health. Workers can use wearables to access information, technical documents, and virtual support. They can also use voice commands to collect data while doing manual tasks. Wearables lead to improved efficiency and decision-making. The IIoT provides a wider view and a deeper understanding of industrial processes by integrating different sensors, wearables, software, and data processing tools.
A few of the industrial monitoring wearables used are Fitness trackers, smart rings, smart glasses, patches/ sensors attached to the body, smart clothing, implantable wearables, Smart bracelets, smart clothes, smart boots, digital pedometers, Smart glasses, helmets, heads-up displays, etc.
Factors to be considered for Industrial Wearable Devices
Industrial wearables comprising various sensors capable of measuring/capturing human vital information that can be easily worn on, or taken off from the human body. These can also be included in body-worn accessories or clothing. They are considered essential tools for precision health. Wearables are found to eliminate or reduce the risk of physical and mental accidents in workplaces. For example, a few wearables monitor the distance between workers and machines. These devices warn the user if the worker approaches too close to the machines.
The functions of industrial wearables can be classified into four groups: monitoring, tracking, supporting, and training. These provide a classification of the metrics collected by wearables to better understand the potential role of wearable technology in preserving workplace safety. Wearables facilitate communication between workers, simplify information management, train workers, and monitor their location parameters.
The functions included in wearables include a pedometer, heart rate monitoring, sports performance tracking, bio-potential measurement, bio-impedance measurement, and blood oxygen measurement. Information on the vital parameters provides the employer and the employee an idea of the latter’s readiness for the work process from a physical and psychological standpoint. Knowing environmental parameters, such as the radiation and temperature at the worksite, allows an organisation to control the factory environment, prevent emergencies, and prepare an effective evacuation plan. Wearables can also be embedded in Personal protective equipment (PPE) to fulfill a protective function.
A few of the design considerations for wearable devices are:
- They should be small in size and lightweight.
- They should consume little power and use efficient connectivity technology. Low quiescent current chip design is suitable for extended standby time.
- These devices must be highly reliable as they must work in various environments. Good mechanical design is a must.
- The device should possess multisensory fusion with low power.
- It must have low-power Bluetooth and Wi-Fi connectivity to access other smart devices.
Smart clothing solution
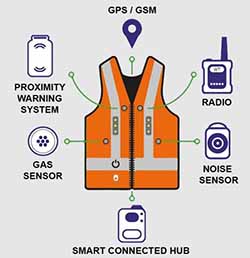
Smart clothing is the terminology for electronic devices that use various sensors to communicate with connected devices (such as smartphones) and the wearer’s body. This product helps minimise risk, ensure safety, maximise control, and improve productivity. Smart clothing complies with applicable government legislation. Figure 1 shows a smart clothing solution.
Smart garments connect workers, their supervisors, and also their site offices. These sensors work together on a single platform to provide alerts, track and report. Sensors in smart clothing include brain activity measuring electrocardiogram (ECG) headbands, and heart straps worn on the chest, posture monitors for detecting posture, and sensors that measure blood pressure, blood flow, pulse, blood oxygen levels, muscle movement, body fat, and body weight.
Sensors used in wearables
Wearables can have different types of sensors depending on the target application. Different sensors collect different kinds of data, which can be digital or analogue-based ; the sensors collect data about the physical or chemical properties of the body and environment, providing insightful feedback. Biometric sensor measures heart rate, heart rate variability (HRV), galvanic skin response (GSR) or blood pressure; environmental sensors provide temperature, pressure or UV light data. A 3-axis accelerometer, gyroscope, magnetometer, and barometric altimeter are some of the motion sensors, and human interface sensors measure proximity, gesture or position.
Wearable technology
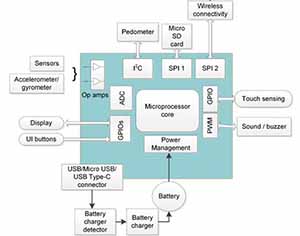
A wearable healthcare device is an autonomous, noninvasive system performing a specific medical function such as monitoring or support. Wearables must satisfy two basic requirements for any IoT device, namely, meeting communications solutions and can access the Internet. They have become one of the most important IoT concepts, forming the Internet of Wearable Things (IoWT) as a promising growing segment.
The core architecture for a smart wearable device consists of a combination of a microprocessor or microcontroller, or similar IC. It has a few micro-electromechanical sensors (MEMS), small mechanical actuators, Global Positioning System (GPS) IC, Bluetooth/cellular/Wi-Fi connectivity to collect/process and sync data, imaging electronics, rechargeable or primary cell (non-rechargeable) battery or battery pack and Support electronics. Digital interfaced sensors are controlled using standard communication, such as I2C or serial peripheral interface (SPI). Analogue sensors need an AFE (Analogue front end) consisting of operational amplifiers (op amps), filters, and analog-to-digital converters (ADCs) to convert the analog signal to a digital signal that the microcontroller can then process.
Figure 2 depicts a generic block diagram of a wearable device. The primary functional blocks are shown, such as the CPU, analogue front-end (AFE), sensors (digital and analogue), display, power management, audio, and networking blocks.
Wearables can use various communication protocols, including Wi-Fi, Bluetooth Classic, ZigBee, and company-specific proprietary interfaces. Many OEMs opt for proprietary protocols as they are energy efficient. Wireless communication protocols are characterised by different performances in terms of transmitting/receiving distance, data throughput, and power consumption. Bluetooth Low Energy (BLE) can achieve minimal possible power for short-range communication. It uses substantially less power whilst maintaining a high data throughput (24 Mbps). ZigBee extends the operational range to 1500m in line of sight whilst consuming less power. Data throughput, however, is restricted to 1 Mbps. Conversely, LoRa combines low power consumption with a high operative range (up to 10 Km in rural areas) but low data throughput (50 kbps).
Power-saving techniques
A wearable that runs out of power is not desirable under any circumstances. Battery lifetime is a vital issue in wearable devices. The energy provided by the battery is limited, and thus there is a limit on the system lifetime before battery recharging or replacement is needed. The device can efficiently manage power in different ways.
- The wearable can switch the controller from active to sleep mode and vice-versa. The device should use the active mode only during data acquisition and processing. Power saving modes include idle and sleep modes, where different peripherals and even the main CPU power off for minimum power consumption.
- Other power-saving techniques include the choice of a suitable acquisition frequency and accuracy in the analogue to digital conversion.
- Asynchronous logic extends the concept of clockless circuits. This approach uses a protocol between functional blocks to indicate when the result from one block is valid for the next, rather than synchronising everything to a clock edge.
- Other power-saving techniques include voltage and clock scaling. The process reduces both when there is low processor demand. This addresses active power consumption, whilst standby, sleep, and deep sleep modes focus on static power.
- Techniques to reduce static power include clock and voltage gating, which removes the clock and/or supply rail from blocks of circuitry when they are not in use, and no power consumption takes place.
Advantages of wearable devices
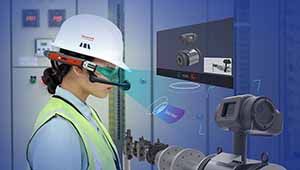
Wearables increase turnover and improve the supply chain by setting new efficiency standards. Technology transforms the way employees work and solves many industry challenges.
- Wearable devices offer secure transmission, storage, display of information and fast access to notifications.
- Goods don’t collide as wearables can track objects and proximity detection sensors avert industry accidents.
- Labour can be easily distributed between operating sites as sensors can observe workers and equipment in real time.
- The safety manager can efficiently organise evacuations since the location of every employee is known. There is an adequate distribution of help and workforce, and you can prevent unauthorised access to the worksite or equipment.
- Some wearable devices can provide a detailed analysis of the actions performed by the worker. The individual can analyse the mistakes to prevent any re-occurrence.
Role of virtual reality (VR) and augmented reality (AR) in industrial Wearables
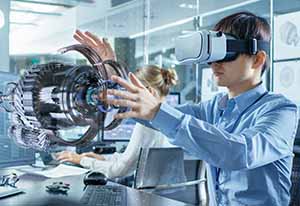
AR is utilised in a variety of industrial solutions, including assembly, part selecting and kitting, testing and inspection, training, and maintenance, amongst others, to show virtual step-by-step interactive visuals onto any work surface using a combination of display and vision sensors. AR allows for the construction of virtual diagrams and graphs, which aid in worker comprehension. Personnel can be trained on complex tasks using VR and AR helmets before performing them in reality. This reduces the risk of damage and provides valuable hands-on experience. Work instructions using guided AR solutions can include fast inspections at any step without affecting cycle time. These technologies facilitate not only the training aspect but also the daily operations of industries that can significantly impact the growth of the organisation.