Lean manufacturing principles can play a crucial role in the electric vehicle (EV) industry in India. The application of lean manufacturing can enhance operational efficiency, reduce waste, and improve overall productivity in EV manufacturing plants. Lean manufacturing is an approach that focuses on maximizing efficiency, reducing waste, and optimizing processes within a manufacturing system. It has gained significant importance in the electric vehicle (EV) industry worldwide, including India. The Indian EV industry is rapidly growing, and implementing lean manufacturing principles can help enhance productivity, quality, and competitiveness. Here are some key areas where lean principles can be beneficial in the EV industry:
Value Stream Mapping (VSM): VSM helps identify and eliminate non-value-added activities, reducing waste and improving process flow. By implementing VSM in EV manufacturing, companies can streamline their production processes, optimize material flow, and eliminate bottlenecks, resulting in increased productivity and reduced lead times. Work-in-process (WIP) limits on the kanban board helps team manage capacity. With this information, it’s now quite easier to see and eliminate normal sources of process waste, returning focus to the customer.
Just-in-Time (JIT) Production: JIT is a core principle of lean manufacturing that aims to eliminate waste by producing and delivering components or materials just when they are needed in the production process. JIT can help EV manufacturers reduce inventory costs, minimize storage space requirements, and improve cash flow by avoiding excess inventory.
Standardized Work: Implementing standardized work processes ensures consistency, reduces errors, and facilitates continuous improvement. In the EV industry, standardized work can be applied to assembly lines, quality control processes, and maintenance activities, leading to improved efficiency and product quality.
Error-proofing (Poka-Yoke): Error-proofing techniques, also known as poka-yoke, involve designing processes and systems in a way that prevents or detects errors before they occur or reach the customer. Implementing such measures can significantly reduce defects, rework, and warranty costs.
Continuous Improvement (Kaizen): Encouraging a culture of continuous improvement is essential in the EV industry to identify and eliminate waste, inefficiencies, and defects. By implementing Kaizen practices, such as employee involvement, problem-solving techniques, and regular process audits, EV manufacturers can drive innovation, increase productivity, and enhance overall product quality.
Total Productive Maintenance (TPM): TPM focuses on equipment reliability and aims to minimize equipment downtime, defects, and breakdowns. In the EV industry, implementing TPM practices can help ensure maximum availability of manufacturing equipment, reduce maintenance costs, and optimize production output.
Employee Involvement and Training: Engaging and empowering employees is vital for lean manufacturing success. Providing training and involving employees in process improvement initiatives can lead to increased motivation, innovation, and a greater sense of ownership amongst the workforces. Companies can establish cross-functional teams or suggestion systems to encourage employee involvement in problem-solving and waste reduction efforts.
Pull System: The pull system turnover the script by emphasizing and helping co-workers finish current tasks before they start the new ones. Throughout the process, when one piece is done, workers notify one another, and the next person can work on the project as soon as their available capacity allows. As a result, morale, productivity, and efficiency get a boost.
Supplier Collaboration: Lean principles extend beyond the manufacturing facility to the entire supply chain. Collaborating closely with suppliers can help streamline the inbound logistics, reduce lead times, improve quality control, and ensure timely delivery of components, enhancing overall efficiency in the EV manufacturing process. Lean manufacturing takes you a little closer to customers because they become the top priority. Visualize what could help your team become more systematic and put lean systems in place to find success. By implementing lean manufacturing principles, the EV industry in India can achieve cost savings, improved quality, increased productivity, and a more sustainable production process. It is important for companies to assess their specific manufacturing processes, identify areas for improvement, and tailor lean practices accordingly to maximize their benefits in the context of the EV industry.
About the Author:
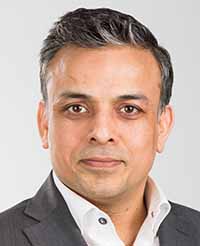
Pankaj GoyalThe author is the Co-Founder & COO of AutoNxt Automation (https://autonxt.in) India’s First electric tractor venture and an automation technology startup.