Saving Energy & the carbon footprint – THE topic of our time! SMART solutions and new approaches show that energy saving measures can result in targeted synergy effects in the production process. SMT Wertheim approaches things differently than others do. With great success and award-winning solutions like “Profiling Plus” (Winner of the Productronica Innovation Award 2021)
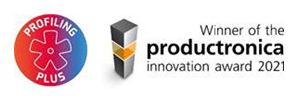
Improvement of insulation What applies to houses and infrastructure projects also applies to the latest generation of SMT Wertheims Reflow systems – developed and assembled “Made in Germany”. With improved insulation, they achieve a significant reduction in heat loss to the outside. With a reflow soldering system with a heating zone length of 3.6m, an average of 1kWh of energy consumption can be saved.
Optimization of heat transfer Once a system has reached the desired profile temperature, most of the energy is from now on required for the heat transfer process into the product. Mechanical energy can be saved through the optimized adjustment of the fan speeds – in a total of fewer heating zones than it is the case in other systems on the market.
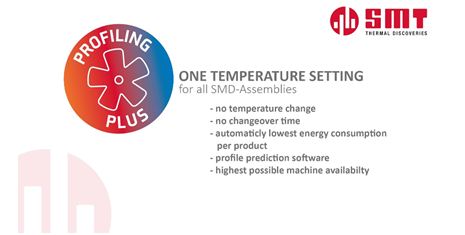
In numbers: SMT Wertheim Reflow Ovens are able to reduce energy consumption of the fans by around 20% with a fan frequency of -6Hz (an R360 reflow system with a heating zone length of 3.6m serves as the basis for the calculation).
Consistent process parameters – without changeover timesA reflow system runs at its maximum efficiency when it is heated up (profile temperature has been reached) and is in continuous operation. To avoid changeover times and thus also energy losses, SMT has implemented the award-winning profile system “Profiling Plus” that guarantees continuous operation with just one temperature setting – regardless of the product. The customer’s heaviest product serves as a reference for the temperature setting.
The precise regulation of the heat transfer is adjusted via the performance of the fans – this is possible within a few seconds. Each product can go through the production process at the same temperature setting. This enables the producer always to achieve the lowest possible energy consumption per product. Changeover times (repeated heating up or cooling down times) are avoided.
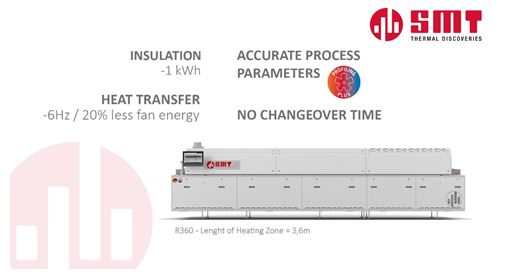
Process gas cleaning / flux managementNo operator and producer likes to open the “black box” reflow soldering system. In general, this is associated with maintenance or cleaning procedures and therefore also with downtimes. To minimize all of this, the reflow systems from SMT Wertheim use the energy-efficient principle of process gas cleaning.
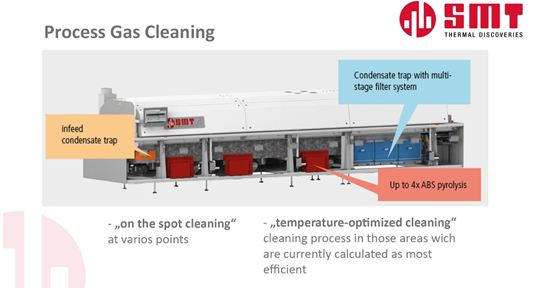
Three-step process gas cleaningInfeed condensate trap – preheating zoneAs soon as the PCB enters the process chamber – a comparatively cooler part of the system – contamination is caught in filters during the preheating process of the components by means of condensation. If necessary, these can be replaced without tools in a few minutes. The process gas cleaning takes place in the peak zone.
CATalysis – ABS pyrolysis in the peak zoneDefinition: Catalysis is the change in the kinetics of a chemical reaction using a catalyst. This change in kinetics activates or accelerates a chemical reaction such as the splitting of long hydrocarbon chains or their oxidation. This process also takes place in the catalytic converter of a car, where most of the exhaust gases from the internal combustion engine are cleaned in the catalytic converter. The catalyst in the reflow system works in a similar way to the exhaust aftertreatment in the vehicle. The long-chain hydrocarbon chains, which are released during the reflow process in the oven, condense in colder places in the oven and sometimes cause resinous and oily impurities. In the soldering system, air that has already been heated is sucked out of the reflow oven (process chamber) by the process gas cleaning system and passed through the catalyst and heated up at temperatures of up to 500°C and then fed back into the oven (process chamber) in a temperature-regulated manner. The large surface of the catalyst (granules) coated with precious metals ensures an optimal cleaning effect. This process not only reduces maintenance intervals and also downtimes, but also it directly supports the production process with the thermal energy already introduced. The process gas cleaning is therefore part of the entire thermal process including the soldering process.
Condensate trap with multi-stage filter system in the cooling zone As with the inlet to the system, dirt is also caught in a condensation process in a multi-stage filter system in the cooling zone. These can also be replaced without tools and in just a few minutes.
On the test bench Whether it’s a car, a refrigerator, or a soldering machine – the information from manufacturers regarding consumption is often not transparent due to the special “in-house test conditions”. SMT Wertheim has put itself to the test externally and independently – at TÜV Süd.
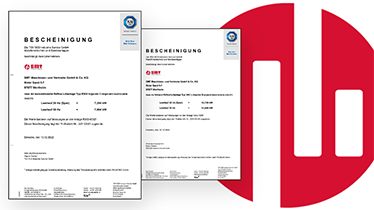
Heating up the system is the most energy-intensive part of the process. Depending on the required profile and the individual product requirements, energy consumption values of 50kWh – 80kWh within the heating-up phase – regardless of the manufacturer and type of system. If the reflow system is ready for operation, however, the consumption values vary greatly.SMT Wertheim is proud to be able to achieve absolute top values in independent consumption measurements by TÜV Süd. A reflow system of the type R360 with a heating zone length of 3.6m and a vacuum reflow system of the type Vac L were tested. To keep constantly low energy consumption values, it is essential to avoid temperature changes. Thanks to SMT’s award-winning Profiling Plus solution, there is no need for this either.
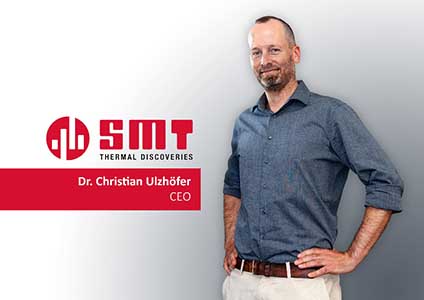
The special relationship with the customer Of course, the business relationship cannot end with the sale of a system. SMT Wertheim supports and looks after their customers long after the moment of commissioning a reflow oven. This ranges from classic after-sales to offering a sophisticated training program to a permanently available range of services. That’s what it’s like when you carry a reliable, long-lasting product from Wertheim out into the world. It is well known that longevity is the first step towards optimizing efficiency….
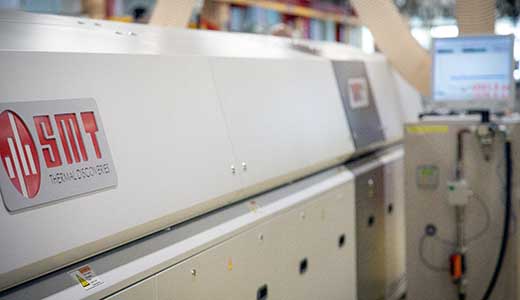