The world needs more power, preferably in a form that’s clean and renewable. Our energy-storage strategies are currently shaped by lithium-ion batteries – at the cutting edge of such technology – but what can we look forward to in years to come?
Introduction
Battery technology has come a long way since the first battery was created by Alessandro Volta in 1800. Early batteries, like the lead-acid battery, were bulky and inefficient, offering limited energy storage. Over the years, advancements such as the nickel-cadmium and nickel-metal hydrate (NiMH) batteries brought improvements in capacity and rechargeability. However, it was not until the development of lithium-ion (Li-ion) batteries in the 1990s that significant breakthroughs in energy density, lightweight design and longevity were achieved. These lithium based batteries became the standard for many portable devices and electric vehicles due to their superior performance and energy efficiency.
We are currently in Generation 3 of battery technologies, specifically in the phase known as Generation 3a. Although some battery systems on the market qualify as “Generation 3”, their performance still falls short of the expectations set for 2030.
Generation 3b, initially considered the next step in improving energy density, remains in its early stages and is not yet ready for implementation. This is also due to the cost, performance and production effort required to develop the samples.
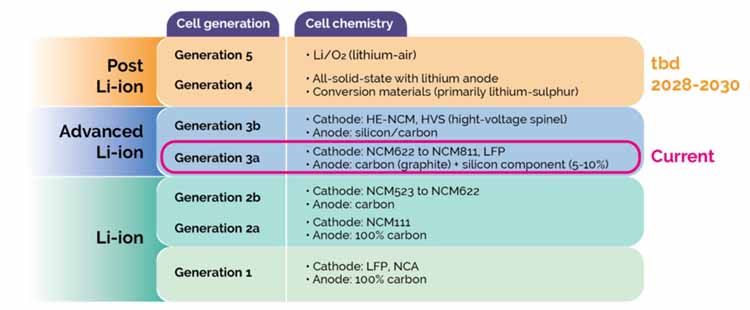
According to Consegic Business Intelligence Next-Generation Batteries Market is estimated to reach over USD 21,143.59 Million by 2030 from a value of USD 13,771.81 Million in 2022, growing at a CAGR of 5.7% from 2023 to 2030.
Next-Generation Batteries Overview:
Next-generation batteries refer to advanced energy storage devices that aim to overcome the limitations of conventional battery technologies. The batteries incorporate innovative materials, designs, and manufacturing processes to enhance energy storage capacity, efficiency, safety, and lifespan. Additionally, these batteries are developed to address the increasing demand for more efficient and sustainable energy solutions in various applications, including electric vehicles, renewable energy integration, portable electronics, and grid-scale energy storage.
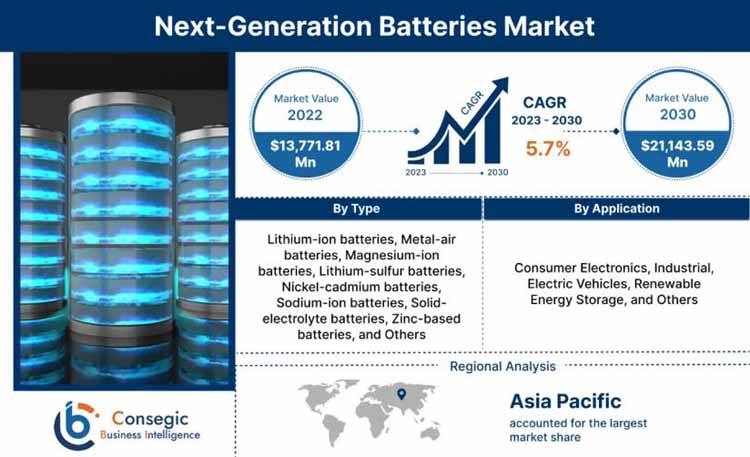
Global demand for Li-ion batteries is expected to soar over the next decade, with the number of GWh required increasing from about 700 GWh in 2022 to around 4.7 TWh by 2030 (Exhibit 1). Batteries for mobility applications, such as electric vehicles (EVs), will account for the vast bulk of demand in 2030—about 4,300 GWh; an unsurprising trend seeing that mobility is growing rapidly. This is largely driven by three major drivers:
- A regulatory shift toward sustainability, which includes new net-zero targets and guidelines, including Europe’s “Fit for 55” program, the US Inflation Reduction Act, the 2035 ban of internal combustion engine (ICE) vehicles in the EU, and India’s Faster Adoption and Manufacture of Hybrid and Electric Vehicles Scheme.
- Greater customer adoption rates and increased consumer demand for greener technologies (up to 90 percent of total passenger car sales will involve EVs in selected countries by 2030).
- Announcements by 13 of the top 15 OEMs to ban ICE vehicles and achieve new emission-reduction targets.
Key drivers of battery innovation
Several factors are driving the rapid advancements in battery technology:
- Increasing Demand for Electric Vehicles: With the global shift towards sustainable transportation, the demand for high-performance, cost-effective batteries for electric vehicles are surging. The demand is expected to grow by around 30 percent, nearing 4,500 gigawatt-hours (GWh) a year globally by 2030, and the battery value chain is expected to increase by as much as ten times between 2020 and 2030 to reach annual revenue as high as $410 billion.
- Renewable Energy Integration: Seen as a more cost-effective alternative to lithium-ion batteries, sodium-ion batteries are being explored for large-scale energy storage. This is where battery technologies play a transformative role. By integrating renewable energy with cutting-edge battery storage systems, India is not only addressing its energy challenges but also creating a robust infrastructure to support its net-zero emissions target by 2070, as pledged at the COP26 summit.
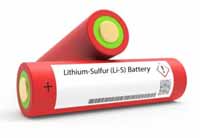
- Lithium-Sulphur Batteries: Offering a significantly higher energy density than lithium-ion, lithium-sulphur batteries have the potential to revolutionise industries like aviation and electric vehicles. Lithium-sulfur battery (LSB) is the future of rechargeable batteries as its theoretical specific capacity and theoretical energy density are much higher than those of conventional lithium ion battery (LIB). Another advantage of LSB is its relatively lower output voltage (2.1 V) which provides higher safety margin.
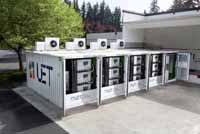
- Flow Batteries: These are suitable for large-scale energy storage, offering scalability and longer lifespans. A flow battery is a rechargeable battery where the energy is stored in one or more electroactive species dissolved into liquid electrolytes. The electrolytes are stored externally in tanks and pumped through electrochemical cells, which convert chemical energy directly to electricity and vice versa, on demand.
- Graphene Batteries: Graphene has a high surface area and capacity which helps to store more ions within its layers. This gives graphene batteries a higher capacity and longer lifetime. Therefore, graphene is an appropriate material for both cathode and anode applications. Electrodes are one of the most influential parts of the battery.
These emerging technologies are paving the way for more efficient, sustainable and scalable energy storage solutions.
Next Generation Battery Materials:
- Silicon Anodes: Silicon-based anodes in Li-ion batteries offer superior electrochemical performance, including higher energy density, greater gravimetric and volumetric capacity, suitable thermodynamic lithiation potentials, and higher average voltage. Today, the use of silicon-based anodes in Li-ion batteries is becoming a reality, with billions of dollars flowing into silicon anode start-ups and a market for silicon anode material for Li-ion batteries projected to reach $24 billion by 2034.
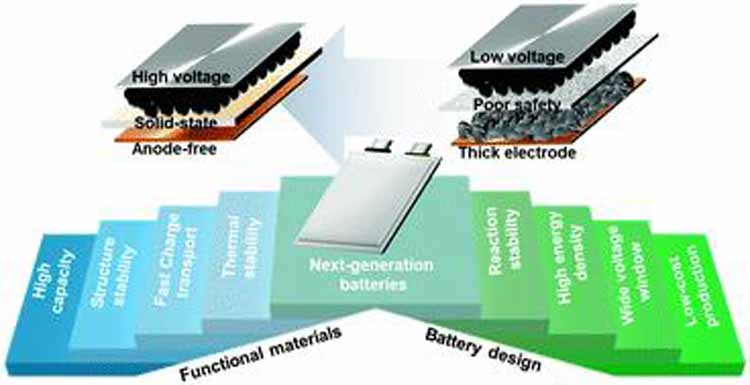
- Lithium-Air Batteries: Lithium-air battery is a type of rechargeable battery that uses lithium metal as the anode and oxygen as the cathode. In theory, it has the potential to have much higher energy density than traditional lithium-ion batteries. Lithium is not consumed during discharge in these batteries, only oxygen is consumed, Total chemical cost of lithium-air batteries – the combined price of cathode, anode and electrolyte materials is about 1/30th the cost of lithium-ion batteries.
- Advance Cathodes: The lithium-ion battery is the most commonly used power battery in new-energy automobiles, which mainly consists of anode material, cathode material, diaphragm, and electrolyte. Cathode materials account for more than 40% of the total cost of lithium batteries, and their performance directly affects the performance indicators of lithium batteries. Therefore, cathode materials play a central role in lithium batteries.
- Organic materials: Organic electrode materials (OEMs) possess low discharge potentials and charge‒discharge rates, making them suitable for use as affordable and eco-friendly rechargeable energy storage systems without needing metals such as lithium or sodium. OEMs can provide a sustainable energy economy by their development into stable and efficient next-generation high-power batteries. Despite the presence of several classes of OEMs, such as conducting polymers, 2D and 3D metal-organic frameworks, organolithium derivatives, 2D covalent organic frameworks, aromatic heterocyclic imides, and viologen derivatives, since their introduction in the 1960s, carbonyl-based molecules have maintained low discharge potentials and stable charging/discharging properties.
The role of Artificial Intelligence in Battery Development
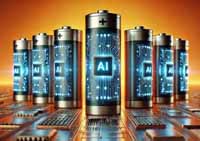
Artificial Intelligence (AI) is playing a transformative role in battery development. With the help of AI data analyses, the error rate should be significantly reduced in the future. Specialised AI applications carry out automated root cause analyses to identify the causes of quality deviations. In addition, AI applications monitor the condition of the machines in the production line. This allows problems to be recognised at an early stage and avoided through intelligent, proactive maintenance planning. Overall, these AI approaches promise significant increases in efficiency, quality improvements and cost savings that can be realised in the short term. AI algorithms are being used to optimise battery design, enhance performance and predict lifespan by analyzing vast amounts of data from various tests and simulations.
Another starting point for the sensible use of AI in battery development is analysing usage to improve service life. Prof Ralf Herbrich is researching this at the Hasso Plattner Institute (HPI) in the field of ‘AI and Sustainability’ in cooperation with a Berlin start-up. Together, they are developing algorithms that can record various wear factors in batteries and draw conclusions for optimal utilisation. In the case of batteries in electric cars, for example, these factors include driving style, the characteristics of charging processes and temperature windows during charging.
Battery Management Systems (BMS): AI can improve BMS, making batteries smarter by predicting potential issues like overcharging or deep discharge thus enhancing safety and lifespan.
Accelerating Research: AI accelerates the discovery of new materials and helps researches model battery performance under different conditions shortening development timeless.
Optimising Manufacturing: AI driven analytics optimize the manufacturing process, improving yield and reducing costs.
With AIs integration battery development is moving faster with increased precision and more customized solutions for specific applications.
New Battery Technologies that will Change the Future
We need batteries that store more, last longer, and are safer to use. Fortunately, new battery technologies are coming our way.
1. NanoBolt Lithium Tungsten Batteries
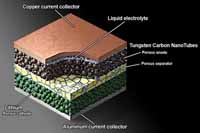
Researchers at N1 Technologies, Inc. added tungsten and carbon multi-layered nanotubes that bond to the copper anode substrate and build up a web-like nano structure. That forms a huge surface for more ions to attach to during recharge and discharge cycles. That makes recharging the NanoBolt lithium tungsten battery faster, and it also stores more energy.
Nanotubes are ready to be cut to size for use in any Lithium Battery design.
2. Zinc-Manganese Oxide Batteries
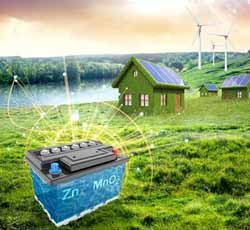
A team based at DOE’s Pacific Northwest National Laboratory found an unexpected chemical conversion reaction in a zinc-manganese oxide battery. If that process can be controlled, it can increase energy density in conventional batteries without increasing cost. That makes the zinc-manganese oxide battery a possible alternative to lithium-ion and lead-acid batteries, especially for large-scale energy storage to support the nation’s electricity grid.
3. Organosilicon Electrolyte Batteries
A problem with lithium batteries is the danger of the electrolyte catching fire or exploding. Searching for something safer than the carbonate based solvent system in Li-ion batteries, University of Wisconson-Madison chemistry professors Robert Hamers and Robert West developed organosilicon (OS) based liquid solvents. The resulting electrolytes can be engineered at the molecular level for industrial, military, and consumer Li-ion battery markets.
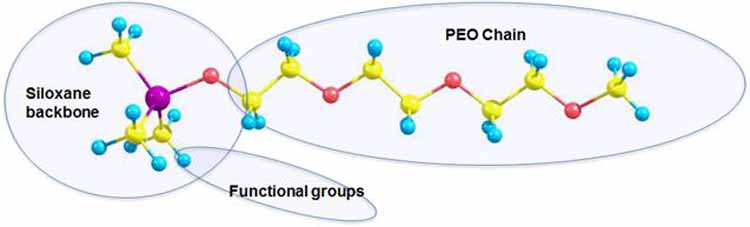
4. Gold Nanowire Gel Electrolyte Batteries
Also seeking a better electrolyte for lithium ion batteries, researchers at the University of California, Irvine experimented with gels, which are not as combustible as liquids. They tried coating gold nanowires with manganese dioxide, then covering them with electrolyte gel. While nanowires are usually too delicate to use in batteries, these had become resilient. When the researchers charged the resulting electrode, they discovered that it went through 200,000 cycles without losing its ability to hold a charge. That compares to 6,000 cycles in a conventional battery.
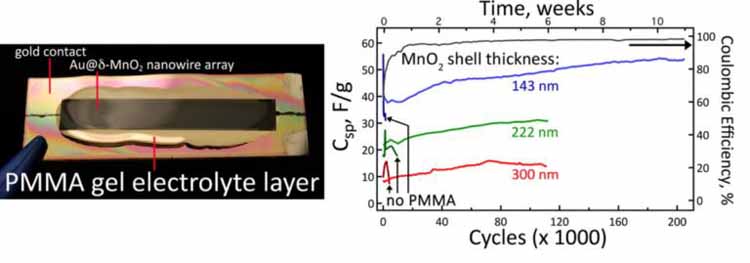
5. TankTwo String Cell™ batteries
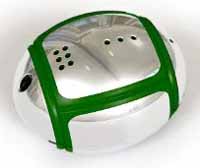
A barrier to the use of electric vehicles (EVs) is the slow recharging process. Seeking a way to turn hours into minutes, Tank Two looked at modularizing a battery. Their String Cell™ battery contains a collection of small independent self-organizing cells. Each string cell consists of plastic enclosure, covered with a conductive material that allows it to quickly and easily form contacts with others. An internal processing unit controls the connections in the electrochemical cell. To facilitate quick charging of an EV, the little balls contained in the battery are sucked out and swapped for recharged cells at the service station. At the station, the cells can be recharged at off-peak hours.
Battery Industry in India
According to Mordor Intelligence analysis Indian Battery Companies Market is Segmented by Technology (Lithium-Ion Battery, Lead-Acid Battery, and Other Technologies) and by Application (SLI Batteries, Industrial Batteries) Motive, Stationary (Telecom, UPS, Energy Storage Systems (ESS), Etc. ), Portable (Consumer Electronics, Etc. ), Automotive Batteries (HEV, PHEV, and EV), and Other Applications).
Indian Battery Market Size
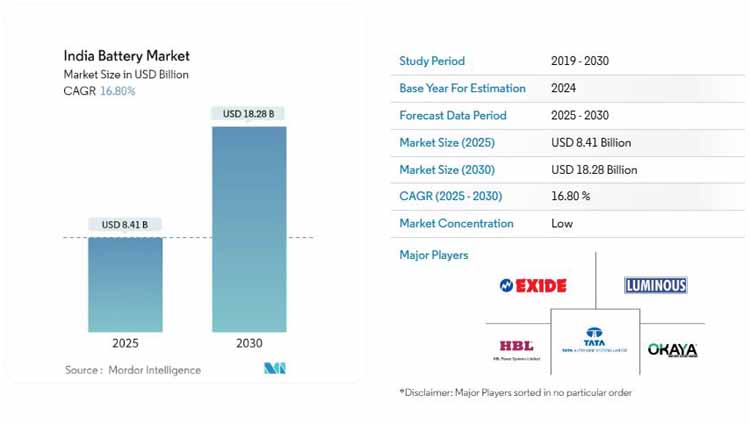
The India Battery Market size is estimated at USD 8.41 billion in 2025, and is expected to reach USD 18.28 billion by 2030, at a CAGR of 16.8% during the forecast period (2025-2030).
Challenges and Opportunities in Battery Manufacturing
Manufacturing Batteries at scale presents several challenges:
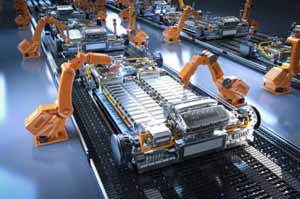
Raw Material Availability: While there are generally enough raw materials available globally to support the growing demand for batteries, the main concern lies in the concentrated geographic distribution of key minerals like lithium, nickel, and cobalt, which could lead to potential supply chain disruptions and price fluctuations if not managed effectively; with countries like Australia, Chile, and the Democratic Republic of Congo holding significant reserves of these materials.
Recycling and sustainability: Lithium-ion batteries, integral to EVs and various electronics, have a finite lifespan. Upon reaching the end of their lifespan, they pose environmental risks due to hazardous materials such as lithium, cobalt, and nickel. Without proper recycling, these batteries can end up in landfills, releasing toxic substances into the environment.
Cost of Production: The primary cost challenges in battery manufacturing stem from the high cost of raw materials like lithium, cobalt, and nickel, which are often subject to supply chain disruptions and price volatility, alongside the need for complex and specialized manufacturing processes, significant capital investment in equipment, and the need for skilled labor to ensure quality and safety, all contributing to high production costs per battery unit.
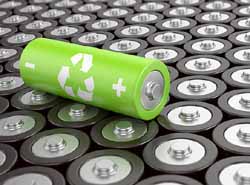
Recycling Technologies: Recycling plays an important role in the overall sustainability of future batteries and is affected by battery attributes including environmental hazards and the value of their constituent resources. Therefore, recycling should be considered when developing battery systems. New methods for recycling battery materials could reduce dependence on raw materials and make the process more environments friendly.
Cost Reduction: The demand for batteries for energy storage is growing with the rapid increase in photovoltaics (PV) and wind energy installation as well as electric vehicle (EV), hybrid electric vehicle (HEV) and plug-in hybrid electric vehicle (PHEV). Electrochemical batteries have emerged as the preferred choice for most of the consumer product applications. Cost reduction of batteries will accelerate the growth in all of these sectors. Advances in manufacturing techniques such as automation and economies of scale are expected to reduce battery costs every time.
Sustainability: There is an increasing drive to move Co-free electrodes for Li-ion batteries. In the global shift towards sustainable energy sources, the battery industry is at the forefront. However, the industry’s rapid expansion comes with sustainability challenges that need urgent attention:
- Resource Extraction: The extraction of raw materials like lithium, cobalt, and nickel, essential for battery production, often leads to environmental degradation. Sustainable manufacturing can mitigate these impacts through recycling and more efficient use of resources.
- Waste and Hazardous Material Management: The manufacturing process generates substantial waste, including hazardous materials. Embracing sustainability means focusing on waste reduction, responsible disposal, and minimizing environmental harm.
Innovations focused on using abundant, non-toxic materials and creating recyclable batteries are vital for the industry long term viability.
Impact of Electric Vehicles on battery Tech: Electric vehicles (EVs) have significantly impacted battery technology by driving demand for higher energy density, faster charging batteries, leading to challenges in battery manufacturing, primarily related to the need for large quantities of critical minerals like lithium, cobalt, and nickel, resulting in supply chain disruptions, price fluctuations, and environmental concerns from mining operations; additionally, concerns around battery recycling and ensuring safe manufacturing processes remain key issues.
Battery Size and Efficiency: Balancing energy density with physical size constraints, managing heat generation during high power applications, optimizing materials to achieve high capacity while maintaining longevity, ensuring consistent quality across different battery sizes, and addressing the trade-offs between cost and performance when scaling up production to meet diverse needs.
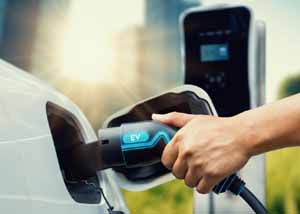
Charging Infrastructure: Electric vehicle (EV) manufacturers are racing to bring new models to the market but face multiple challenges, such as meeting the demand for shorter charging times or reduced battery weight. Fulfilling safety requirements, Safeguarding quality and Rising costs some major ones
Battery Recycling: With the increasing number of EVs there is a greater need for efficient battery recycling systems to handle the lifecycle of batteries.
Conclusion
The future of battery technology seems bright, with many exciting, innovative developments on the horizon. Future batteries will store more energy in smaller and lighter packages. Next-generation batteries are expected to charge faster, enabling more convenient usage for consumers. Continuous Innovations will result in batteries that last longer, reducing the need for frequent replacements and contributing to sustainability to meet the global energy demands.