From detecting tool wear to enabling automatic tool changes, sensors play a vital role in the implementation of smart tooling methodologies for CNC machines. But how can manufacturers ensure that these sensors are up to scratch? In this article, Ross Turnbull, Director of Business Development and Product Engineering at ASIC design and supply specialist Swindon Silicon Systems, explores the benefit of custom ICs in intelligent tooling applications.
Incorporating sensors and connectivity features within tooling solutions, otherwise known as smart tooling, allows manufacturers to benefit from real-time data and automation capabilities, helping to improve overall production efficiency.
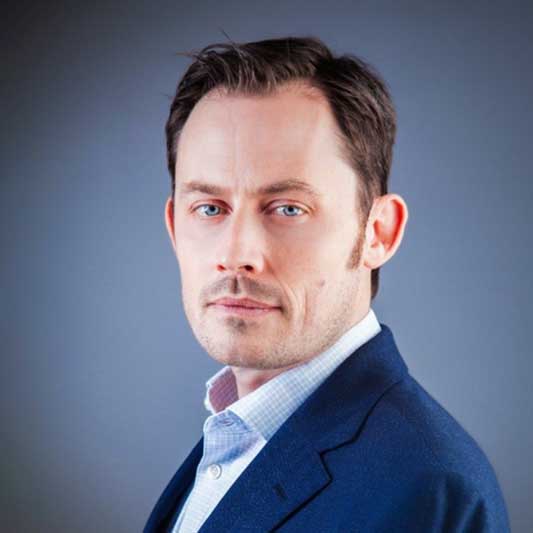
Measuring wear and tear
An increasingly common use of sensors within CNC machines is for tool wear monitoring. Measuring and predicting tool wear helps to limit product quality issues caused by the degradation of cutting tools over time. However, monitoring methods such as microscopes and laser devices require machining to be paused to inspect the tools, therefore increasing downtime and production costs.
In contrast, sensor technology offers a more time-efficient means of ascertaining tool condition. One example is the micro-electro mechanical system (MEMS) accelerometer, which is commonly used to measure changes in vibration patterns during machining. Understanding vibration can help manufacturers to avoid detrimental changes to surface quality and tool geometry.
Piezoresistive MEMS accelerometers measure vibration using a cantilever beam with a proof mass at its end and a piezoresistive patch in the beam’s core. When the device moves, inertia causes the beam to bend, altering the mass distribution of the silicon wafer. This deformation generates an electrical signal, proportional to the object’s acceleration.
Integrating these sensors into the tooling system can help to detect subtle changes in tool geometry and wear patterns, allowing manufacturers to schedule tool replacements before failures occur, thereby reducing scrap rates and maintaining product consistency.
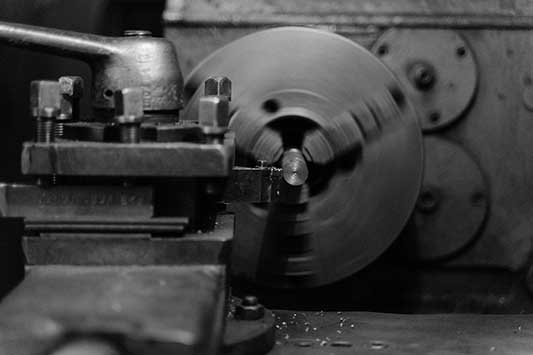
Smarter tool changes
Sensors are also indispensable within the automatic tool change (ATC) systems that are used on CNC machines used for different types of material processing, such as switching between milling and grinding.
ATC systems help to reduce the likelihood of human error and accidents associated with manual tool changes. Their benefits extend beyond safety, contributing to increased flexibility in production, enabling manufacturers to handle a wider range of materials and components with minimal reconfiguration.
A wide range of sensors are implemented to guarantee the accuracy and reliability of an ATC operations. Two common examples are position sensors and proximity sensors.
Position sensors provide feedback on the position of three core machine components: the magazines used to store cutting tools, the grippers that hold and release the tools during changeover and the holders that connect the cutting tool to the spindle. Meanwhile, proximity sensors identify whether a tool is correctly seated in the grippers.
ASIC advantages
To fully unlock the possibilities of smart tooling, manufacturers looking to develop sensor-driven machining technologies must consider the role of application-specific integrated circuits (ASICs).
Unlike off-the-shelf ICs, ASICs can be tailored for the exact demands of individual applications. This customisation results in high-performance, cost-effective solutions that integrate seamlessly with advanced machining systems.
For instance, ASICs enhance the performance of MEMS accelerometers in CNC machines by providing customised signal conditioning to optimise tool wear monitoring. By integrating ASICs, the accelerometer’s signal processing is fine-tuned to improve accuracy and noise resistance, ensuring more reliable tool condition data.
The fully optimised chip design of an ASIC eliminates unnecessary components, enabling more power to be focused precisely on the features that matter most for smart tooling applications. This streamlined design ensures that position and proximity sensors can provide accurate and reliable placement feedback.
A further benefit of opting for an ASIC over a standardised IC is that it provides superior protection against obsolescence. With off-the-shelf chips, there is a risk that production will cease if sales volumes fall and producing the part is no longer financially viable. However, since ASICs are designed exclusively for a customer’s application, providers can guarantee that a supply will be available for the lifetime of that specific product.
Incorporating ASICs into smart tooling systems offers significant advantages, from enhancing sensor performance to ensuring long-term reliability. With the ability to customise for specific applications, ASICs provide optimal solutions that improve efficiency, reduce downtime and protect against obsolescence, making them an essential component for futureproofing CNC machinery.