In 2021, the automotive industry witnessed an essential shift as solid-state devices like the VIPower M0-7 H-Bridge became the primary drivers of DC motors. Powered trunks, window lifts, sunroofs, sliding doors, seat and mirror adjustments, and more rely on DC motors. Moreover, new applications, such as deployable door handles, e-shifters, and EV chargers, also use these systems. And while many of these features used to be only for luxury models, they are now considered mainstream. Interestingly, one consequence of this industry shift is the obsolescence of relays as DC motor drivers in favor of solid-state devices. Hence, let us explore how engineers can benefit from solid-state drivers and overcome significant design challenges.
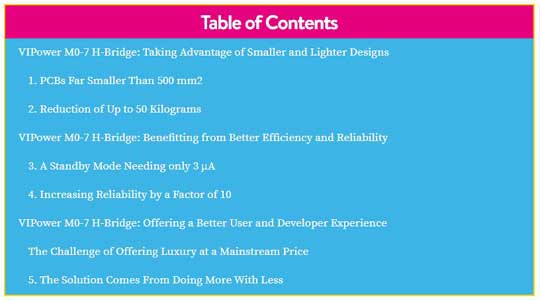
VIPower M0-7 H-Bridge: Taking Advantage of Smaller and Lighter Designs
1. PCBs Far Smaller Than 500 mm2
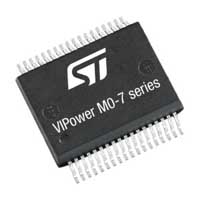
Most engineers chose devices like the VIPower M0-7 H-Bridge because they are fully integrated motor drivers offering monitoring and protection features in a single package, thus opening the door to vastly smaller PCBs and greater efficiency. For instance, a typical 250 mm2 relay implemented in an H-bridge topology traditionally demands a PCB of 500 mm2. Additionally, a larger surface area needs more components and is thus more prone to malfunctions. Hence, designers turned to solid-state drivers to create smaller, more cost-effective designs.
2. Reduction of Up to 50 Kilograms
The VIPower M0-7 H-Bridge comes in a tiny SO-16N or PowerSSO-36 package. The smaller footprint of each device (60 mm2 and 106 mm2, respectively) and their thickness under 2.5 mm enable the creation of significantly smaller. Moreover, the ST lead-free packaging offers greater thermal dissipation, alleviating the need for a heat sink. Similarly, the presence of monitoring and protection functionalities limit the number of external components needed and help optimize cable sizing around the car. As a result, between the absence of heat sinks, the reduction in cables, and the overall optimizations, the VIPower M0-7 bridges can help reduce weight by up to 50 kg per vehicle.
VIPower M0-7 H-Bridge: Benefitting from Better Efficiency and Reliability
3. A Standby Mode Needing only 3 µA
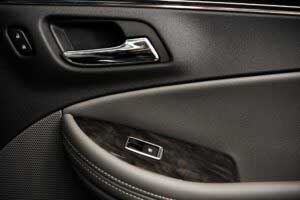
Solid-state drivers are inherently more efficient, but the VIPower M0-7 H-Bridge pushes things further. For instance, its standby mode only needs 3 µA, while some competing devices are into the double digits. Similarly, the ST device has a low quiescent current to increase efficiency further, while optimized switching profiles ensure that the motor driver’s power consumption remains low. Put together, all these benefits not only improve power consumption but the car’s environmental impact. Indeed, thanks to a vastly more efficient and lighter vehicle, manufacturers can improve fuel economy to reduce CO2 emissions or increase battery life for a longer overall range between charges.
4. Increasing Reliability by a Factor of 10
Readers of the blog already encountered ST’s VIPower in systems like our Adaptive Front Lighting Solution. Indeed, the VIPower series has already proved its high reliability in the automotive market, which explains why it’s in a significant number of design wins. The reliability also comes from the VIPower M0-7 H-Bridge’s ability to reduce the number of external components necessary. Designers can do away with snubbers, diodes, and amplifiers. As a result, the PCB is simpler, increasing reliability by a factor of 10 compared to a similar solution using relays.
VIPower M0-7 H-Bridge: Offering a Better User and Developer Experience
The Challenge of Offering Luxury at a Mainstream Price
Consumers are increasingly demanding a more luxurious experience from their mainstream vehicles. As a result, OEMs try to match expectations by enhancing the user interface and infotainment systems. Cars also include more and more controls. Everything is customizable, movable, connected, and smarter. Hence, the challenge for engineers is to bring these features without blowing up costs. Finally, electric vehicles pose a new challenge. As EVs aim for a more futuristic user experience and highly focus on power consumption, there include up to four times more solid-state drivers than a car with an internal combustion engine.
5. The Solution Comes From Doing More With Less
Devices like the VIPower M0-7 H-Bridge offer various profiles and control over PWM signals to provide a smoother ride experience. Through the MultiSense pin, teams can monitor Vcc voltage, package temperature, load current or perform advanced diagnostic analysis. The off-state diagnostics can check standby conditions and detect a short to the battery or an open connection, thus avoiding potential damage when starting the DC motor. The VIPower M0-7 H-Bridge also offers a wide range of on-state resistance (from 8 mΩ up to 100 mΩ), which means that engineers can work with a lot of loads from a few watts to 200 W).
Thanks to the reliability and efficiency of devices like the VIPower M0-7 H-Bridge, powered trunks, and automatic sunroofs are now present in consumer cars. By offering more diagnostic, engineers can ensure a far longer lifespan. Similarly, the wide range of on-state resistance means using the same component in a far greater number of designs. Teams only need to qualify one device, thus vastly lowering costs. Reducing the design’s footprint also means carmakers can put more features onto the same space. Ultimately, a device like the VIPower M0-7 H-Bridge shows how solid-state drivers have transformed the automotive industry.