Rehm is a trusted supplier to our own electronics works, and countless SIMATIC components owe their superior quality at least in part to the outstanding performance of the ovens and solutions from Rehm Thermal Systems. SIMATIC is returning this favor as the preferred PLC in Rehm’s convection soldering solutions.
Convection soldering systems from Rehm are considered to be among the best. And the quality, precision, performance, and efficiency of Rehm systems have been one of the keys to the process performance and quality of the electronic works in Amberg, which manufactures to a quality standard of 99.9990% (a fact, not a boast). Together, Siemens and Rehm have designed and developed some of the game changers in reflow soldering, such as the VisionXP QuadLane – a reflow convection soldering system with a four-lane conveyor that increases production capacity while reducing footprint requirements by 30%. This long and trusted collaboration is now entering a new phase: Rehm will not only help make SIMATIC components but will also use SIMATIC controllers as preferred systems in its convection soldering systems.
A Decision Based on Experience
The move to SIMATIC did not come out of the blue – Rehm Thermal Systems has for years been equipping some of its machines with SIMATIC systems, depending on the specifications of the supplier, so the decision was based on ample experience. It was the quality of the SIMATIC controllers that has always impressed Wolfgang Zeifang, CTO of Rehm Thermal Systems:
Whenever we delivered a machine with a SIMATIC controller, we knew we would probably never hear of any controller issues. – Wolfgang Zeifang, CTO of Rehm Thermal Systems
With the new TIA Portal engineering system and the new series of SIMATIC controllers, specifically the SIMATIC ET 200SP distributed controller, Rehm quickly realized that this system could offer even more benefits through an integrated yet scalable platform.
A Global, Long-Term Perspective
Rehm’s soldering systems are high-volume products with many options and versions, so the company needed an automation system that could be tailored to specific performance requirements, and the SIMATIC range provides that capability. Moreover, TIA Portal enables efficient engineering for teams, which aligns with the engineering process and organization at Rehm. SIMATIC systems are used globally and backed by a reliable service and support network all over the world, which benefits Rehm’s international customers. And last but not least, all components are available over the long term, which supports efficient life cycle management for machines and systems, both in the field and within the Rehm engineering team.
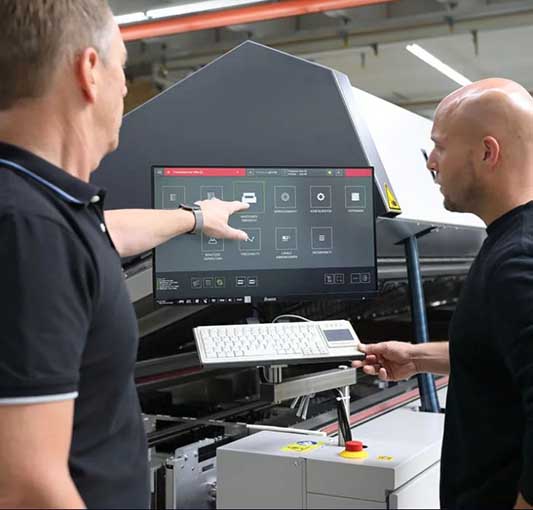
A straightforward transition
With the first SIMATIC controllers delivered and installed, Rehm is already seeing the value of the new automation standard. The members of the engineering team were able to build on their existing SIMATIC knowledge to transfer the programs and options for the soldering machines into the new engineering system – a process that is not yet complete, “but we’re making good progress,” as Markus Mittermeier, head of software development at Rehm, confirms. When this process is complete, Rehm expects to benefit from added savings and synergies in projects.
What’s next?
In the meantime, Rehm is already working with Siemens on new ideas and plans. Specifically, data integration and applications for the Industrial Internet of Things are focus areas for Rehm – and with SIMATIC, the company has chosen a range of systems that already supports many industry standards for data integration and communication. “We need to be able to provide excellent data visibility to our users, both in machines and across lines, and we need to achieve that with minimal manual integration. This is why we are very much interested in working with Siemens on solutions that use standards such as Hermes, and it is very reassuring to have a partner that is like-minded and working in the same direction,” says Mittermeier.
So, how does it feel to use controllers that were made by your own machines, in those machines? The question is met with a big smile from the team at Rehm and a simple answer: “Good!” The feeling is mutual: “Rehm has been a trusted supplier of reflow ovens to Siemens for almost 30 years, so we have used virtually all generations of Rehm systems here in our EWA (Electronic Works Amberg). This long cooperation has grown into a long-term and strategic partnership in which both parties – supplier and customer – are working on standards and optimization strategies together. Such collaboration is beneficial not just for the Amberg plant but for all of Siemens’ electronic works. With this in mind, the entire team at the EWA feels very proud that Rehm not only uses our own SIMATIC portfolio on request for our thermal systems but now also intends to use SIMATIC controllers in all of its systems. Another major standardization milestone!,” declared Bernhard Erras, Strategic Planner SMT Manufacturing, Siemens.
What is your feeling about SIMATIC as a standard solution in SMT? Where could you see SIMATIC aiding your manufacturing? Please let me know in the comments – or check out our website for more information.