Industrial robots are essential to modern manufacturing — executing a vast array of functions while coordinating tasks with other forms of automation. In fact, the $1T automotive industry was the first industry with the means to make large-scale use of robotics … and advance the technologies associated with robotics as well. No wonder, as automobiles are highly sophisticated big-ticket items that can justify plant investments that may not yield ROI for years. Now, the vast majority of automotive manufacturing centers employ robotics. Only over the last two decades have the fields of packaging, semiconductor production, and the relatively new field of automated warehousing hastened their robotics adoption to rival the automotive industry.
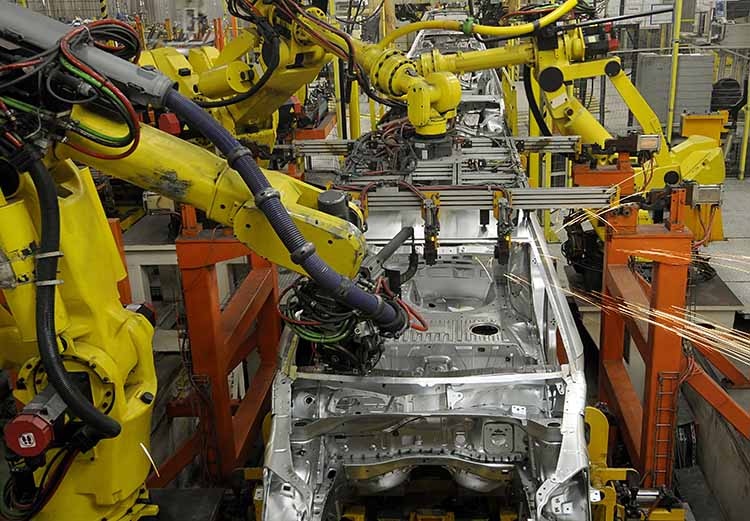
Within robots themselves and in complementary industrial-automation equipment are electric motors, hydraulic systems, and fluid power systems; drives, controls, networking hardware, human-machine interfaces (HMIs), and software systems; and sensing, feedback, and safety components. These elements impart efficiency by executing preprogrammed routines that can readily adapt to changing realtime conditions. Increasingly, it’s expected that robotic workcells also feature reconfigurability to produce new automobile offerings … as consumer preferences have come to evolve more rapidly than ever.
Clarifying terminology used for automation and robotics
The Oxford English Dictionary defines robots as “machines capable of automatically carrying out complex series of movements, esp. programmable.” Confusing matters is that this definition could describe everything from washing machines to CNC machine tools. Even the ISO 8373 definition of a robot as an “automatically controlled, reprogrammable, multipurpose manipulator, programmable in three or more axes” could describe a warehouse conveyor with vertical lift stations. However, such machines would never normally be classified as robots.
The practical differentiator to remember is that machines built for a single [read: very clearly defined] use in a fixed location aren’t usually considered robots … at least not in industrial circles. For example, although a typical milling machine can run any number of complex programs to machine different parts, it’s designed to cut metal using rotary blades mounted in its spindle … and it’s likely to remain securely fixed in a single location for its entire service life.
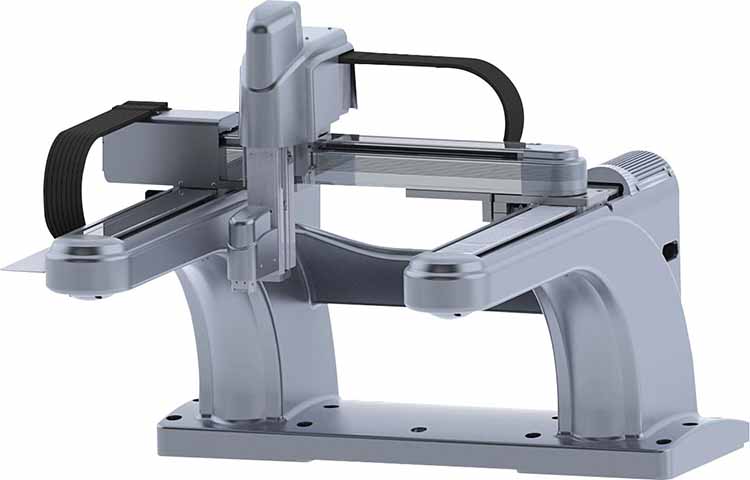
Sometimes, even these definitions are contradicted. For example, automated machines such as CNC machine tools are increasingly flexible, with mill-turn centers performing the roles of both milling machines and lathes — and many such machines executing inspection and measurement tasks on parts with contact probes and laser scanners as well. Such machine tools may even be equipped to perform additive manufacturing. On the other hand, supposedly flexible industrial robots are often supplied as specialized models designed for a specific task such as paint spraying or welding … and may well spend their entire service life parked within one workcell on a production line.
The bottom line is that in the automotive industry today, automated systems classified as robots are indeed often expected to exhibit high flexibility — capable (with reconfiguration) of executing transport, sorting, assembly, welding, and painting tasks that may vary day to day. These industrial robotics are also expected to be relocatable to new areas in a plant — whether for redeployment as manufacturing systems and reconfigured or continually movable on seventh-axis linear tracks to service workcell arrays in a line.
Robot Families for Automotive Production Sites
Robots in automotive production sites are broadly classified by their mechanical structures — including their joint types, linkage arrangements, and degrees of freedom.
Serial manipulator robotics include most industrial robots. Designs in this design family have a linear chain of links with a base at one end and an end effector at the other end … with a single joint between each link in the chain. These include articulated robots, selective compliance articulated robot arm (SCARA) robots, collaborative six-axis robots, cartesian robots (essentially consisting of linear actuators), and (somewhat uncommon) cylindrical robots.
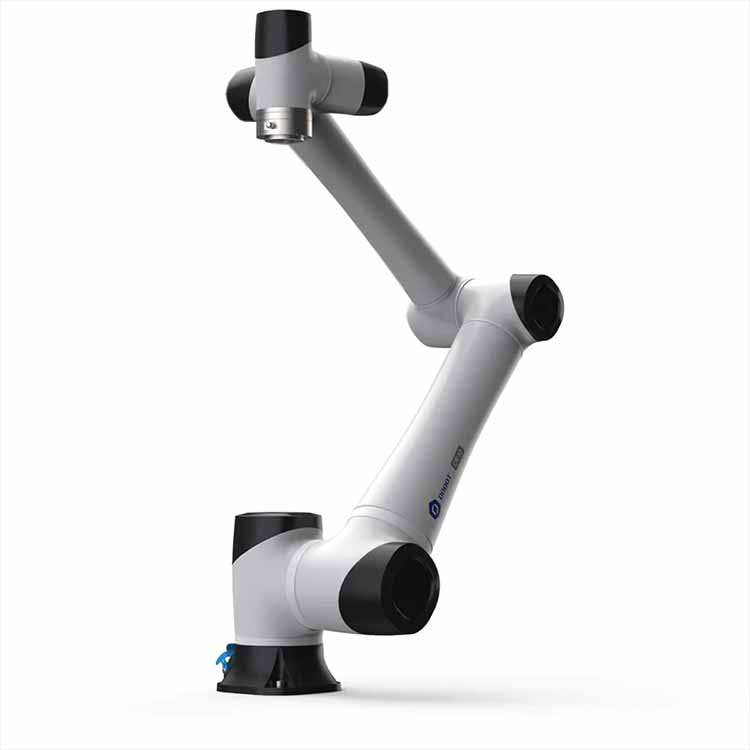
Parallel manipulator robotics excel where applications need high rigidity and operational speed. In contrast with articulated arms (suspended in 3D space via a single line of linkages) parallel manipulators are supported or suspended by arrays of linkages. Examples include delta and Stuart robots.
Mobile robotics are wheeled units that move materials and stock items around factories and warehouses. They may function as automated forklifts to retrieve, move, and place pallets on shelving or the factory floor. Examples include automated guided vehicles (AGVs) and autonomous mobile robots (AMRs).
Classic Robot Uses in Automotive Manufacturing
Classic robotic applications in automotive manufacturing facilities include welding, painting, assembly, and (for the transport of the 30,000-odd parts that go into the average car) material-handling tasks. Consider how some robot subtypes are put to use in these applications.
Six-axis articulated arm robots are serial manipulators in which every joint is a revolute joint. The most common configuration is the six-axis robot having degrees of freedom to position objects in any position and orientation within its working volume. These are very flexible robots suited to myriad industrial processes. In fact, six-axis articulated arm robots are what most people picture when thinking of an industrial robot.
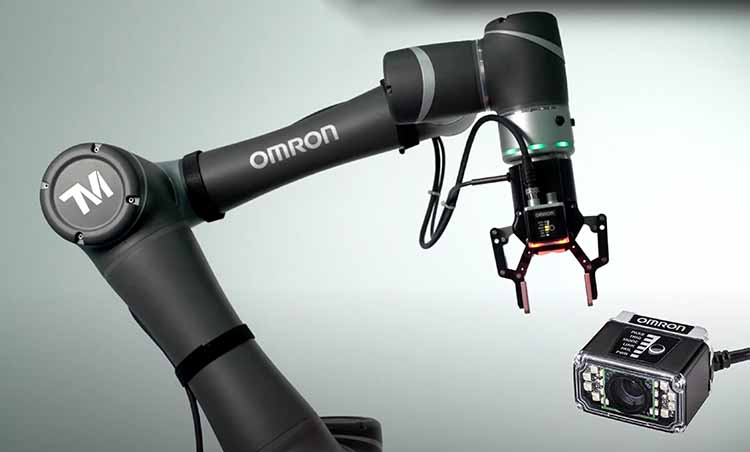
In fact, large six-axis robots are often used in automobile frame welding and spot welding of body panels. In contrast with manual approaches, robots have the ability to precisely trace weld paths in 3D space without stopping while concurrently accommodating the changing parameters of the weld bead in response to environmental conditions.
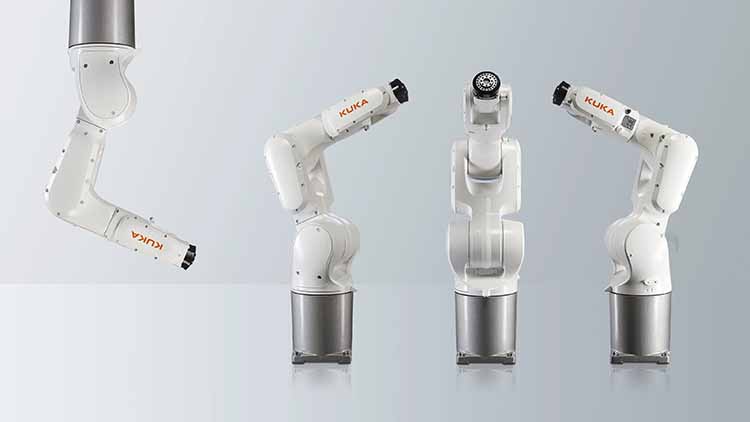
Elsewhere, six-axis articulated arm robots ride on seventh-axis systems to execute priming, painting, clearcoating, and other sealing processes on automobile panel bodies. Such arrangements deliver flawlessly consistent results that are in part so reliable because these processes are executed in well-isolated spray booths effectively kept uncontaminated by particles from the outside environment. Six-axis robots also follow programmatically optimized spray paths for perfect finishes even while minimizing overspray and paint and sealer waste. What’s more, they eliminate the need to expose automobile-plant personnel to the harmful vapors associated with some spray-applied materials.
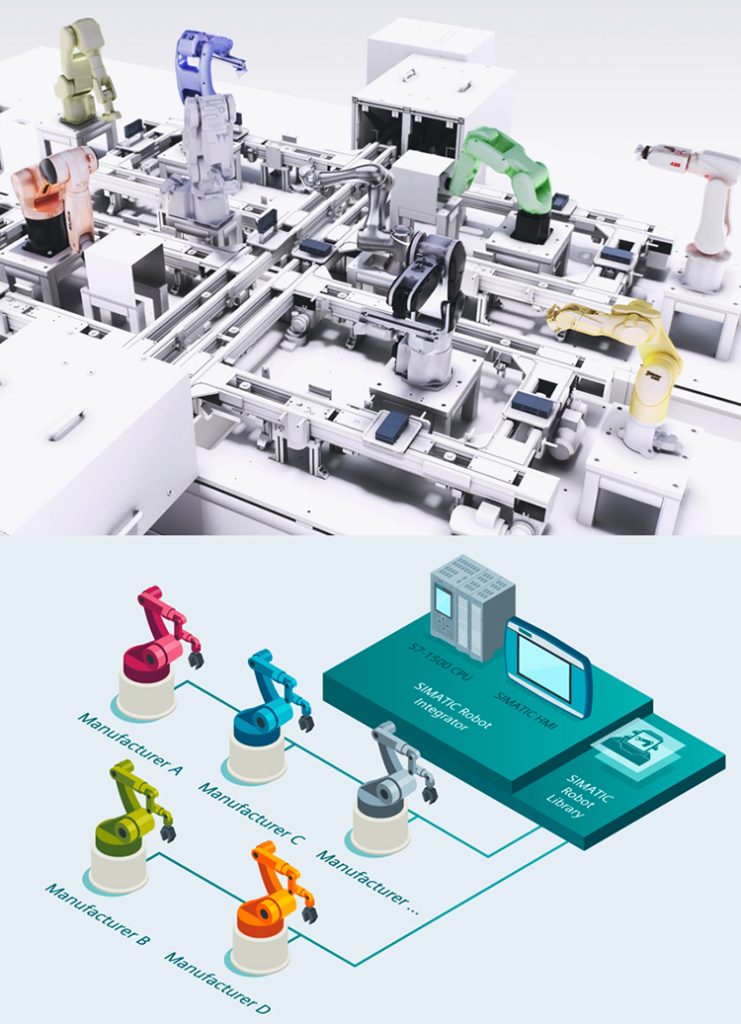
Selective Compliance Articulated Robot Arm (SCARA) robots have two revolute joints having parallel turning axes running in the vertical direction for X-Y positioning in a single plane of motion. Then a third linear axis allows motion in the Z (up and down) direction. SCARAs are relatively low-cost options that excel in confined spaces — even while delivering faster moves than equivalent cartesian robots. No wonder SCARA robots are used in production of automotive electronics and electrical systems — including those for climate control, mobile-device connectivity, audio/visual elements, entertainment, and navigation. Here, SCARAs are most commonly used to execute the precise material handling and assembly tasks to produce these systems.
Cartesian robots have, at minimum, three linear axes that are stacked to execute motion in the X, Y and Z directions. In fact, some cartesian robots employed by Tier-2 automotive suppliers take the form of CNC machine tools, 3D printers, and coordinate measurement machines (CMMs) to verify the quality and consistency of end products. If counting these machines in the tally, cartesian robots are easily the industry’s most common form of industrial robot. As mentioned earlier though, cartesian machines are often only called robots when they are used for operations involving the manipulation of workpieces and not tools — in assembly, pick-and-place, and palletizing, for example.
Another cartesian robot variation used in the automotive industry is the automated gantry crane. These are indispensable for fastening and joining processes requiring access to the undercarriage of partially completed vehicle assemblages.
New and Novel Robot Uses in Automotive Manufacturing
Cylindrical robots are compact and economical robots that give three-axis positioning with a revolute joint at the base and two linear axes for height and arm extensions. They are particularly well suited to machine tending, packing, and palletizing automobile subcomponents.
Collaborative six-axis robots (cobots) mentioned earlier feature the same basic linkage structure as larger industrial variations, but with extremely compact and integrated motor-based drives at each joint … typically in the form of a gearmotor or direct-drive option. In automotive settings, these are tasked with welding brackets, mounts, and geometrically complicated subframes. Benefits include high precision and repeatability.
Delta robots have three arms that are actuated via revolute joints from the base — often mounted to the ceiling for a suspended arrangement. Each arm has a parallelogram with universal joints mounted at its end, and these parallelograms all then connect to the end effector. This gives the delta robot three degrees of translational freedom with the end effector never rotating relative to the base. Delta robots can achieve extremely high accelerations, making them highly effective for pick-and-place operations in applications involving the sorting and other handling of small automotive fasteners and electrical components.
Stewart platforms (also called hexapods) consist of a triangular base and triangular end effector connected by six linear actuators in an octahedron. This imparts six degrees of freedom with an extremely ridgid structure. However, the range of motion is relatively limited in comparison to the size of the structure. Stewart platforms are used for motion simulation; mobile precision machining; crane motion compensation; and high-speed vibration compensation in precision physics and optics test routines … including those to verify vehicle suspension designs.
Automated guided vehicles (AGVs) follow set routes marked by lines painted on the floor, wires on the floor, or other guidance beacons. AGVs typically have a degree of intelligence so they stop and start to avoid collisions with each other and with humans. They are highly suitable for material-transport tasks in automotive-production facilities.
Autonomous mobile robots (AMRs) don’t require fixed routes and are able to make more sophisticated decisions than AGVs. Particularly useful in the sprawling warehouses of automobile manufacture, these typically achieve free navigation using laser scanners and object recognition algorithms to sense their environment. When a potential collision is detected, instead of stopping and waiting like an AGV, AMRs can simply alter course and move around obstacles. This adaptability renders AMRs considerably more productive and flexible in automotive plant loading docks.
Conclusion
The automotive industry has spurred massive innovation in the field of robotics over the last 30 years, and that trend will continue with the burgeoning electric vehicles (EVs) market. The industry has also begun to benefit from new AI and machine vision adaptations to enhance robotic installations for uses of all types.