Although gallium nitride (GaN) has been discussed as an interesting solution for inverters and motor drives for ten years, there have been very few real applications of GaN in this sector to date. However, now that GaN has been proven in other applications, such as chargers, its value proposition is now being seriously evaluated by motor drive manufacturers, and designs are starting to emerge.
The imperative in the charger market that forced the pace of GaN adoption was size or power density. Suddenly, at a stroke, simply by using GaN, chargers could be made smaller and less obtrusive, and their power capability could be significantly increased. Size can be an issue for motor drives too, but not in many cases. For traditional variable-frequency drive (VFD) motors for commercial industrial uses such as pumps and fans, because they do not have an output filter – usually the output is three phase directly connected to a motor winding – there’s no incentive to shrink passives. Therefore, there is no significant benefit to be gained by increasing the switching frequency by using GaN. Also, the motor drives and inverters market is very mature and it can be very cost sensitive.
However, there are new technology trends in the inverter market that GaN can help address, especially in the 100W to 2kW range as the price of GaN is falling.
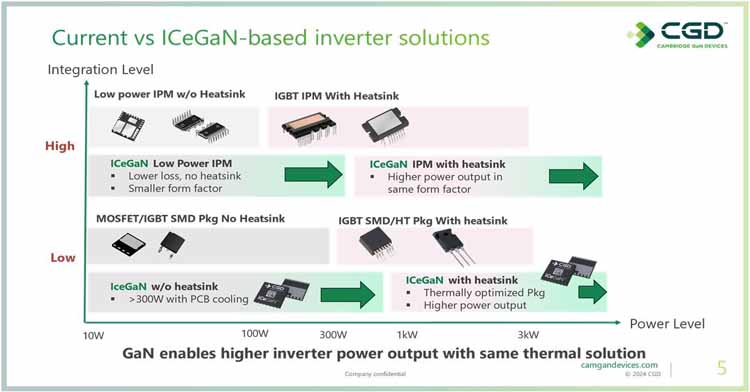
Figure 1 shows that the value proposition of GaN is not simply to shrink the size – although, in some cases, it may be. But GaN enables higher power output within the same package envelope because it generates so much less heat. This means better, simpler, more reliable solutions and higher power levels. This also opens up the practicality of greater levels of integration. In the figure we can see that compared to discrete MOSFET and IGBT designs, GaN extends available power levels up to well above 300W without a heatsink. If the heatsink can be removed, then of course as well as size, weight will be reduced, and cost, reliability and manufacturability can be improved. However, if the power demand is higher – say a few kilowatts – then using GaN with a heatsink means that the power is available. And the beauty of it is, especially in a mature market, that the design does not have to change, you can still switch at 20kHz and motor/inverter designers can stay in their comfort zone. Consider, for example, a 500W motor drive design. Traditionally, this would probably employ an IGBT in a big TO-247 package with a heatsink. But with GaN, you can use a small 8×8 DFN-packaged device, throw away the heatsink and rely on the PCB for cooling.
Then, if we look at IPMs (integrated power modules), which are very popular in some motor drive applications such as air conditioning units and BLDCs in general because of the simplicity and reliability of the solution, it’s the same story: more power in the same form factor package, and less heatsinking.
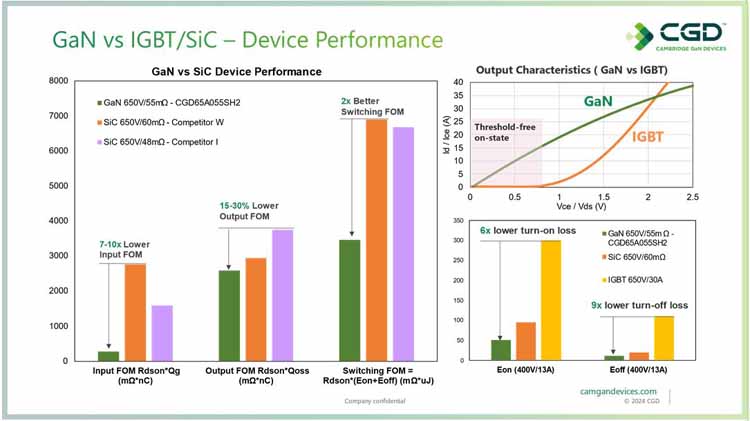
Figure 2 reminds us of the performance benefits of GaN devices versus IGBTs and SiC (silicon carbide).
The analysis versus IGBTs – the traditional solution up to 3kW/650V – shows that GaN has six times smaller turn-on losses and nine times smaller turn-off losses. Also, the low conduction losses of GaN mean that the light load performance of this technology is extremely good. IGBTs have a ‘knee point’ or threshold voltage, so won’t turn on until the system reaches 0.7V. This means that whilst at full load, both IGBT and GaN solutions exhibit high efficiency, at below, say, 20% load the efficiency of the IGBT solution falls off a cliff (Figure 3).
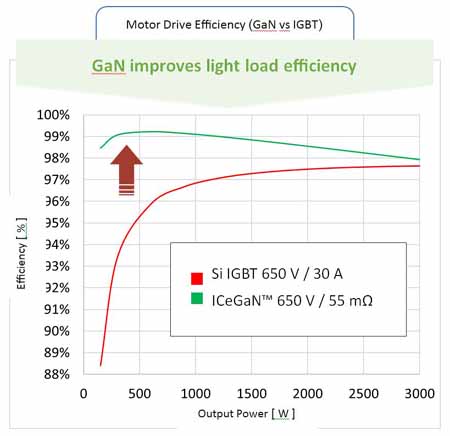
So, to summarize, even at low switching speeds, GaN brings significant efficiency improvements, especially at light loads. This results in a higher power capability and reduced BOM costs by reducing/eliminating thermal solutions such as heatsinks, fans and special substrate materials such as IMS (Insulated Metal Substrate and DBC (Direct Bonded Copper) – simple, inexpensive FR4 will often suffice. This, of course, has huge implications for sustainable design and helps equipment manufacturers meet energy efficiency standards and reduce waste. It also results in a reduced dollars/watt cost equation.
We have said that for many motor drive/inverter designs, system frequency is not important, but in some cases, there can be an incentive to increase the switching frequency. Higher switching frequency can result in: an improved soft and quiet motion profile and control; reduction of audible noise above 20kHz, especially for ceiling fans, heat pumps, refrigerators etc.; and reduction of current ripple and THD.
While IGBTs are limited to around 50kHz, with GaN, of course, there is no problem to increase switching speeds to 100-200kHz.
Why ICeGaN®?
In general, then, we can see that GaN now offers many system-level benefits over IGBT solutions for motor drive and inverter designs up to 3kW. ICeGaN, Cambridge GaN devices’ enhancement mode GaN-on-silicon power transistor technology, offers some added benefits, primarily its ease of use. No special driver is required, the designer can take whatever they have been using to drive their
IGBTs or MOSFETs – literally the same chip – to drive the CGD ICeGaN devices without changing anything. Most IGBTs are driven at 15V: ICeGaN HEMTs can be driven anywhere from 9-20V, so 15V is
right in the sweet spot. This appeals greatly, especially in what we have acknowledged as a mature market. Telling motor drive designers who have been using IGBTs their whole lives that they need to have a very tight loop layout and special 0-6V gate drivers is not going to go down well. In contrast, CGD offers a very simple plug-and-play replacement solution.
Picking up on the point about the layout, Figure 4 shows a 3-phase power stage implemented using IGBTs versus ICeGaN GaN transistors. This design was originally laid out for IGBTs, which – because IGBTs have a slow switching speed – did not need to consider gate loops. In that sense, it’s a very poor design – there is no loop optimisation at all.
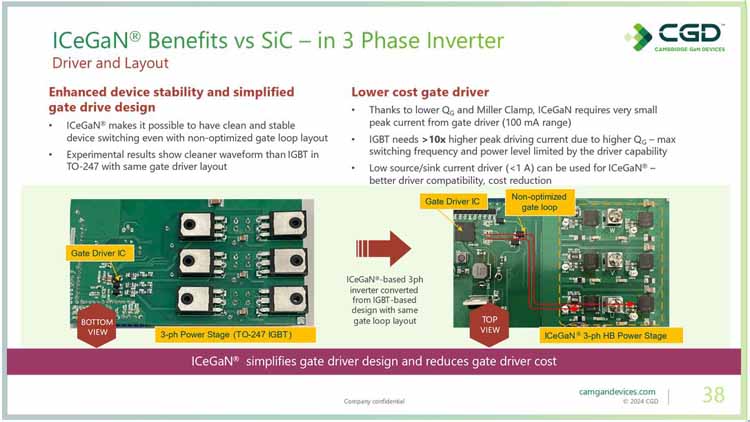
But as can be seen in Figure 5 which shows the output plots of the two boards, the ICeGaN functions very well and has a clean waveform. This is due to the internal Miller Clamp that CGD implements in GaN alongside the switch in its ICeGaN transistors, which holds the gate off internally during off state.
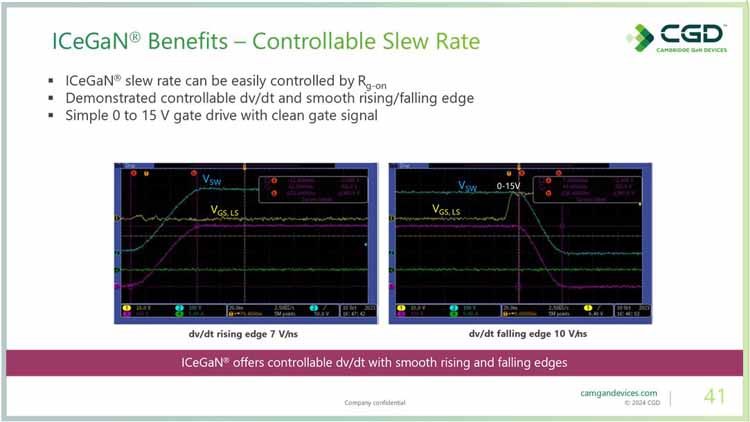
The resulting waveforms show that there is no overshoot or ringing; there is a very clean turn-on VGS. Also, the peak gate driving current is just 100 mA, 10x smaller than with IGBTs. This is important for some designs where the driver is included in the motor drive controller IC. Such drivers are not very strong, providing only 300-500mA, not enough to turn on and off an IGBT. With ICeGaN there is plenty of headroom.
A further benefit concerns current sensing. ICeGaN integrates a current sensing function on chip, eliminating the need for current shunts. Finally, ICeGaN only integrates the interface circuitry, not the driver itself which is the approach chosen by some other GaN companies. The limitation of this latter approach is that it becomes hard to fine-tune the turn-on slew rate dv/dt. ICeGaN looks, in this respect, like a discrete solution and, therefore, is simple to control.
Summary
In conclusion, GaN technology can be applied in motor drive and inverter designs to increase available power, reduce BOM count and cost, and support smoother and quieter motion control by enabling higher switching frequencies. ICeGaN makes all this very simple for designers to implement by delivering a drop-in replacement solution that can use existing drivers and requires no special circuit layout optimization. For any support with GaN in India visit www.supremecomponents.com or dropp an email on pss@supremecomponents.com